News
June 2025:
We have recently completed a Post Processor and Machine Simulation set for one of our key customers.
Click play below to view an animation video:
Star – SR-32JII Type B – Fanuc 32i-B control.
Twin Spindle, Multiple Gang – Swiss Style Turning Centre.
Using Fusion with Advanced FeatureTURN/MILL.
Showing; Turning and Milling Operations,
C Axis Indexing, Milling with Front and Side Tools and Part Transfer Control (Part Off).
All then simulated through FeatureCAM's own Machine Simulation software.
April 2025:
We recently completed a Post Processor and Machine Simulation set for a major defence company.
Click play below to view an animation video:
Nakamura-Tome – MX-100 – Fanuc 31i-B control.
Twin Spindle, Twin Turret – Upper B Axis Head – Turning Centre.
Using Fusion with Advanced FeatureTURN/MILL.
Showing; Turning and Milling Operations,
(C Axis Indexing, Synchronised Milling with Upper and Lower) and Part Transfer Control (Part Off).
All then simulated through FeatureCAM's own Machine Simulation software.
March 2025:
We recently completed a Post Processor and Machine Simulation set for a major defence company.
This is our first double compound wedge Y axis machine.
Click play below to view an animation video:
Okuma – GENOS L3000-e MYW – OSP-P300L control.
Twin Spindle Turning Centre.
Using Fusion with Advanced FeatureTURN/MILL.
Showing; Turning and Milling Operations - C Axis Indexing, Polar Interpolation,
Wrapping and Part Transfer Control (Part Off).
All then simulated through FeatureCAM's own Machine Simulation software.
May 2020:
FeatureCAM 2021 R1 - Is released.
June 2019:
FeatureCAM 2020 R1 - Is released.
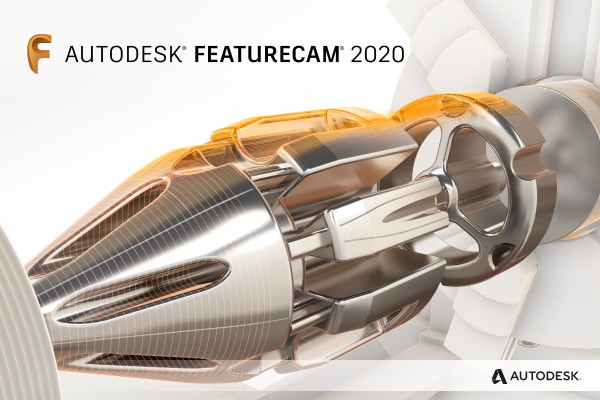
What's new in FeatureCAM 2020
The new features and enhancements added since FeatureCAM 2019.3.4.
Add-in improvements
Align parts in vises along positive and negative axes: When using the Import Vise add-in, you can now orient parts along X+, Y+, Z+, X-, and Y-, instead of just X, Y, and Z. This is useful for double station vises because they can then be reassembled in Multiple Fixture documents.
API improvements
Export as STL: When using the ExportToSTL method, all solids associated with a multi-body solid are exported. Identify holder type: A read-only HolderType property in FMLatheTool and FMThreadTool objects returns the type of holder.
PartMaker
PartMaker 2020: Autodesk® PartMaker is again made available as part of FeatureCAM Ultimate, after an absence in 2019.
Subscription benefits
Subscribing to FeatureCAM offers many benefits, including:
Shared Views
Use Shared Views to collaborate online with people you're working with. You can upload a shared view, which is a visual representation of all toolpaths and solids in a model, from within FeatureCAM. By sending a link to the shared view to your collaborators, they can view, and comment on, the shared view in Autodesk Viewer, without needing an Autodesk product.
Drive
Autodesk® Drive provides a secure location in the cloud for individuals and small teams to store, preview, and share model or design data. View data in Drive from any device with a browser.
Fusion 360
Autodesk® Fusion 360 is a cloud-based CAD/CAM/CAE tool for collaborative product development. Fusion 360 offers a connected design and manufacturing solution, with a range of tools for workflows, from concept exploration to solid modelling to advanced manufacturing.
April 2018:
What's new in FeatureCAM 2019.
Explore new and enhanced features to automate your workflow from design to NC code; reduce programming time; and produce consistent results for CNC milling, turning, and wire applications.
FeatureCAM® 2019 has new capabilities for applying feature recognition. Get enhanced collaboration, a better user experience, and improvements for programming multitasking lathes.
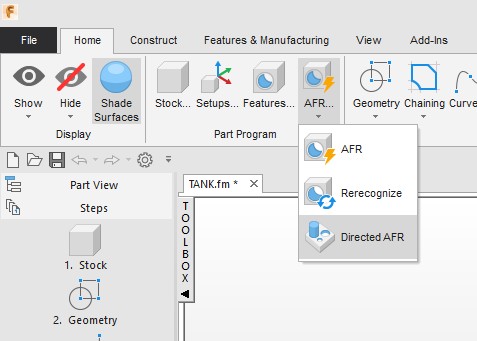
Directed Automatic Feature Recognition (DFR)
Automatically recognize holes, bosses, sides, and pockets for faster programming.
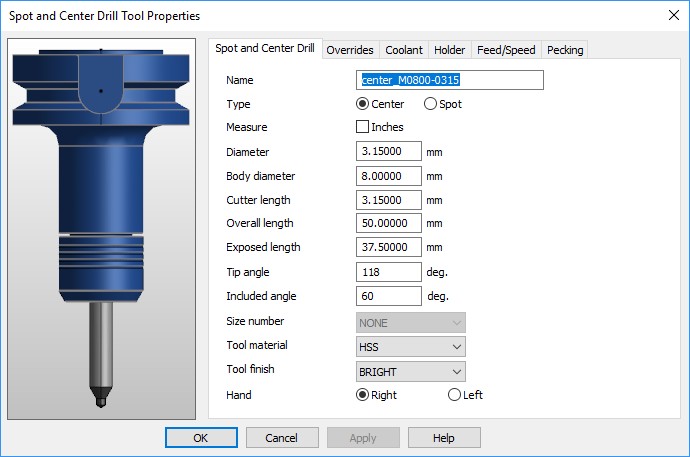
Modify centre drill geometry
Change the tip and included angle of your center drill for accurate simulation and NC code.
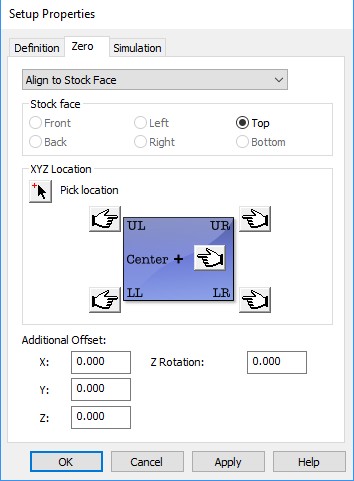
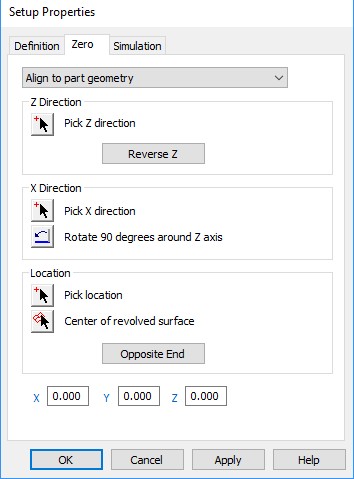
User experience improvements
Including a faster way to create and edit setups, an enhanced thread library, and more.
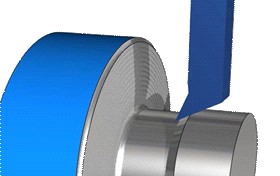
Back cutting
A new turning strategy for specialized inserts, including Sandvik PrimeTurning.
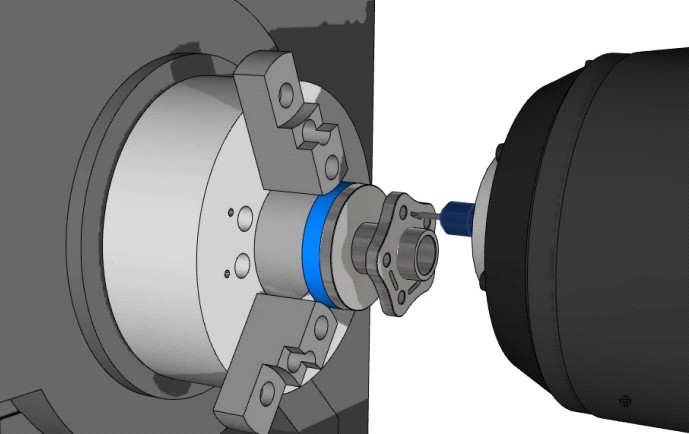
Radial pattern improvements
Machine radial patterns using XY coordinates and rotate the C angle for each instance of a feature.
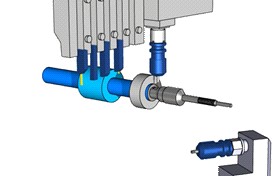
Swiss programming improvements
Ultimate
Including fixed angled holders, creating a thread path from a curve, and more.
December 2017:
FeatureCAM 2018 Product Comparisons.
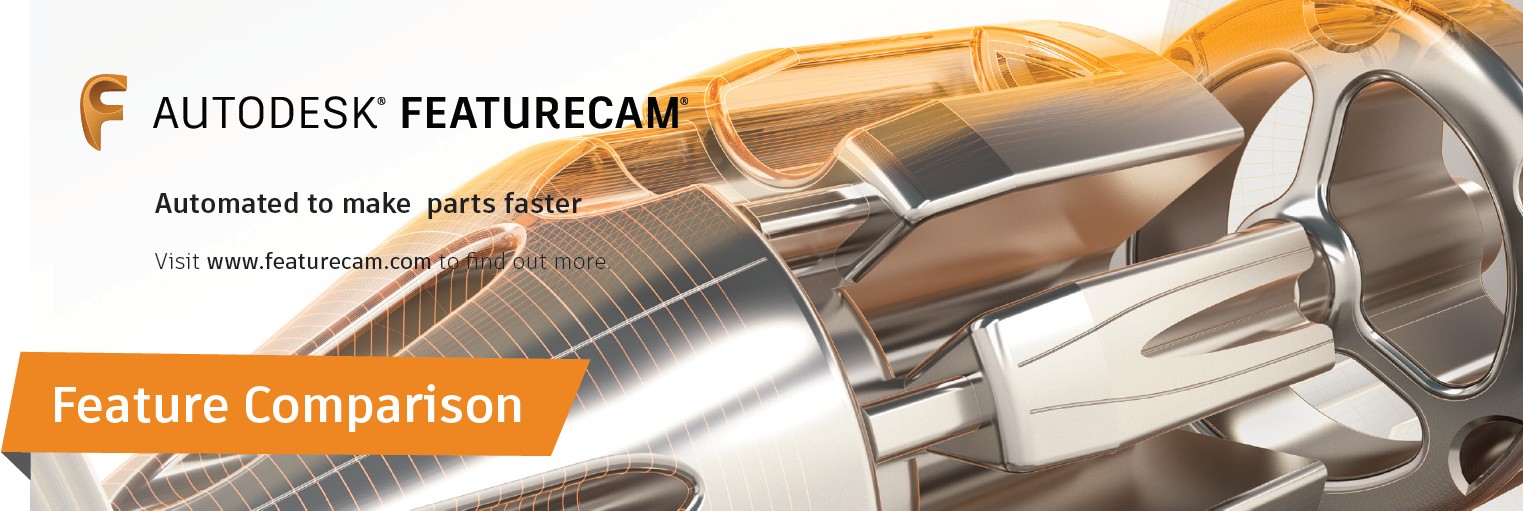
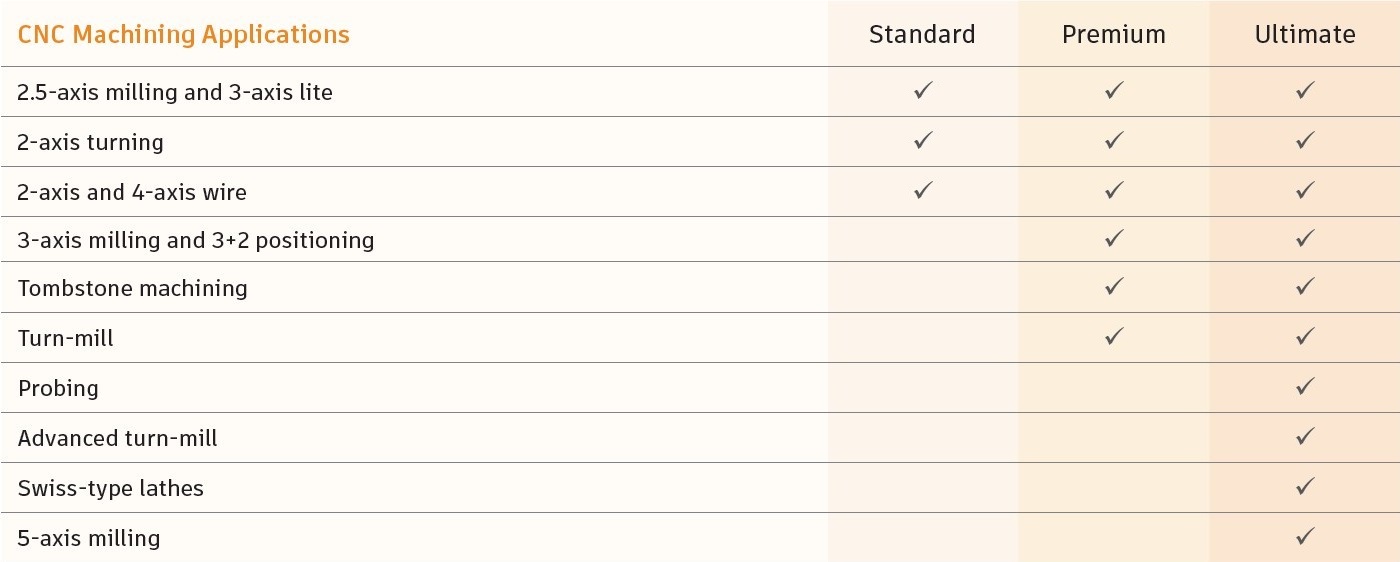


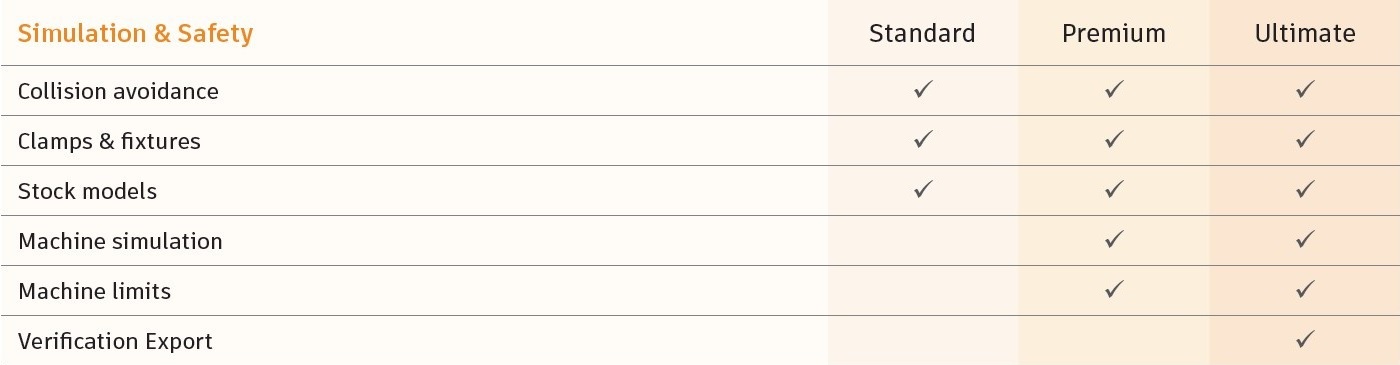
April 2017:
FeatureCAM 2018 R1 - Is released.
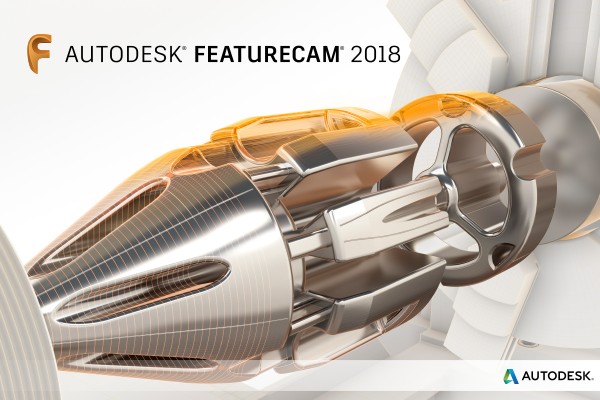
Explore new and enhanced features to automate your workflow from design to NC code; reduce programming time; and produce consistent results for CNC milling, turning, and wire applications.
FeatureCAM® 2018 includes a new user experience including a ribbon interface. Get better interoperability with third-party data, more automation to reduce programming time, and new technology for Swiss-type lathes.
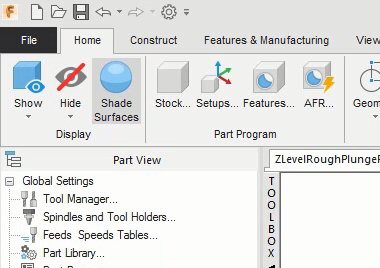
User experience improvements
The most notable change is a new ribbon interface:
• Enhances the look and feel of the software
• An icon, accompanying text and dynamic help give more insight into functionality
• Similar groupings simplify and speed up navigation
• Customizable to create your preferred working environment
In addition to the ribbon:
• A new options dialog makes managing and changing project details easier
• Use the multi-channel editor to view, edit and align multichannel NC programs
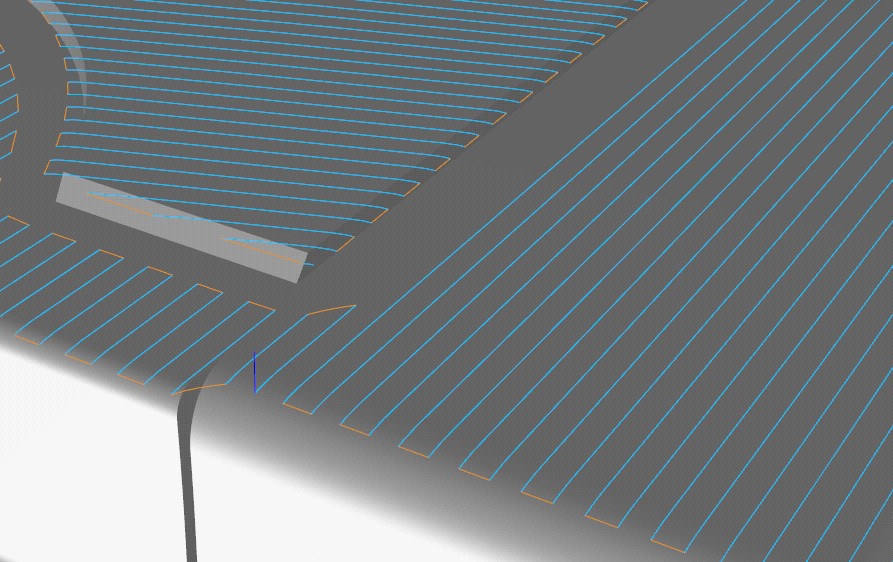
Automatic angle for parallel finishing
Automatically determine the optimum angle for your toolpath, based on the region you are machining. An optimal orientation minimizes the number of tool retracts and helps to create efficient toolpaths from multiple surfaces faster.
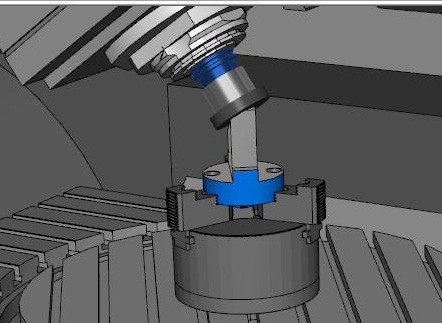
Automatic 3+2 positioning
Use the axis limits of your machine design file to automatically determine either a standard or alternate position. This helps validate your program is within your machine’s working envelope before it is sent to the machine.
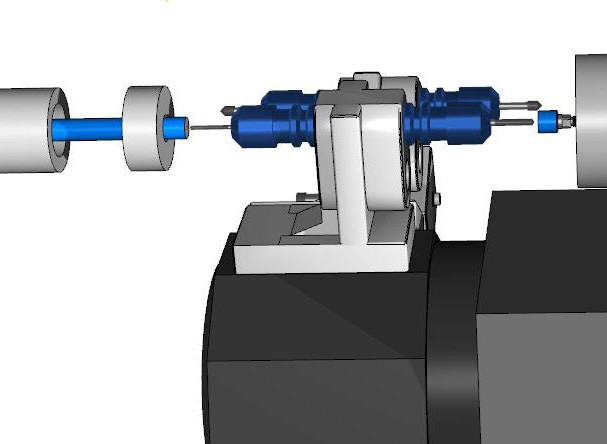
Swiss synchronization
Program and simulate advanced synchronization modes for Swiss-type lathes with superposition and double-end drilling.
This helps to:
• Improve machine usage
• Reduce cycle times
• Improve throughput
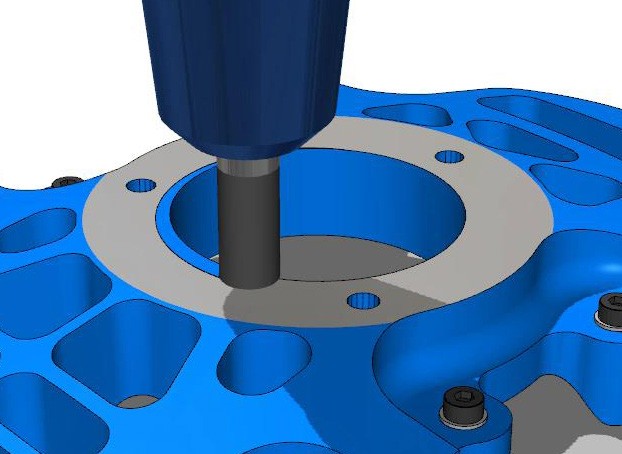
Spiral toolpath improvements
Use an inner boundary curve to constrain your toolpath to the region you want to machine. This creates a shorter toolpath to avoid fresh air cutting.
August 2016:
FeatureCAM 2017 R1 - Is released.
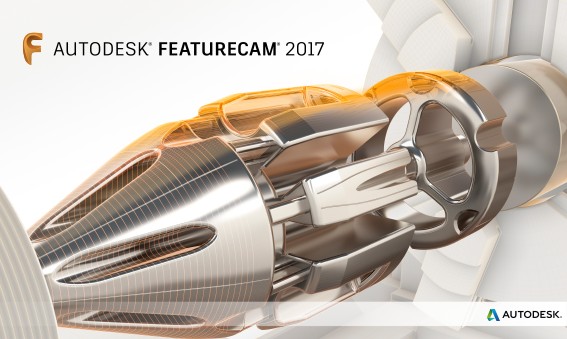
FeatureCAM 2017 R1 delivers a wide range of new features and improvements.
New features and enhancements include:
User Interface Improvements
Product Manufacturing Information
2.5D Improvements
3 Axis Improvements
Turn/Mill Improvements
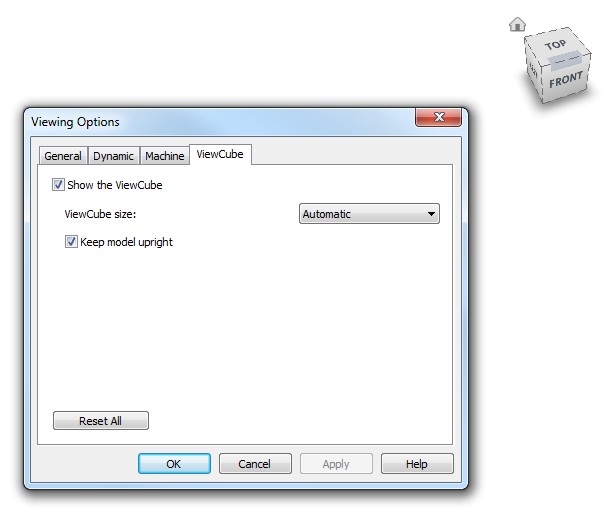
User Interface Improvements
FeatureCAM has received additional improvements to the User Interface. The most notable addition is that of the View Cube. The View Cube can be used to manipulate the view orientation, either dynamically, or by using the fixed views. A customizable home view can be set, with additional options to change the size of the cube and the view scaling.
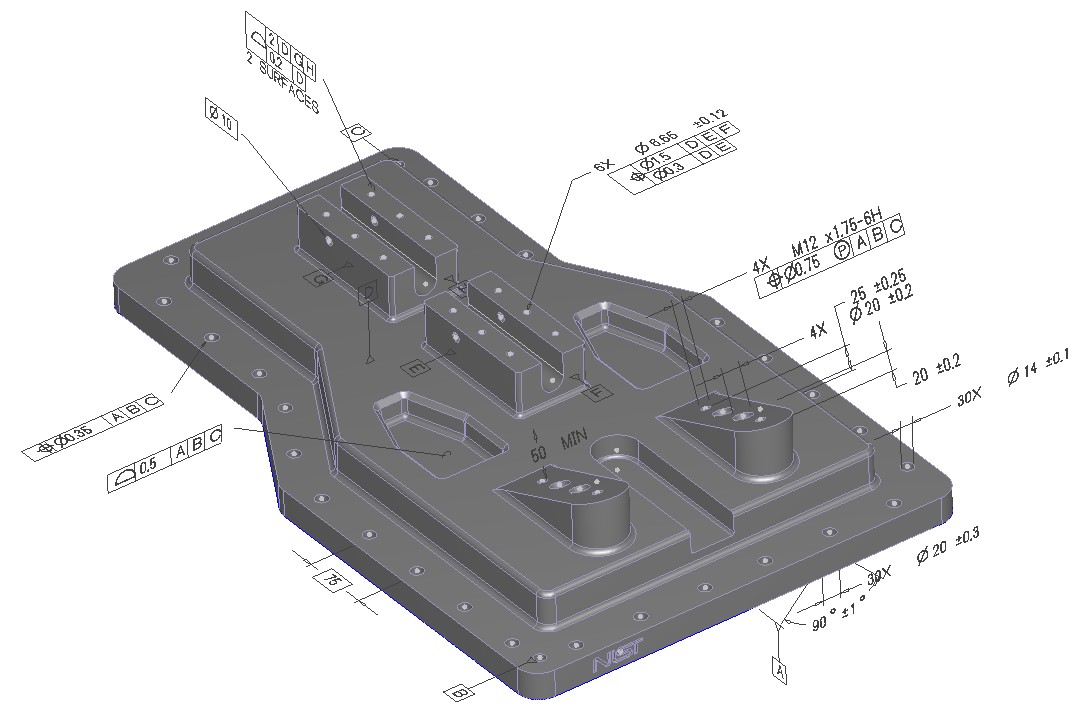
Product Manufacturing Information
Product Manufacturing Information (PMI), which includes the Geometric Dimensioning and Tolerancing (or GD&T), can help you understand the design intent of a CAD file. FeatureCAM therefore provides the capability to import a variety of CAD data formats that contain PMI, either natively, or through the Autodesk Manufacturing Data Exchange Utility. If the PMI features are saved associated with a pre-defined view, these are also imported, and accessible through the User Views.
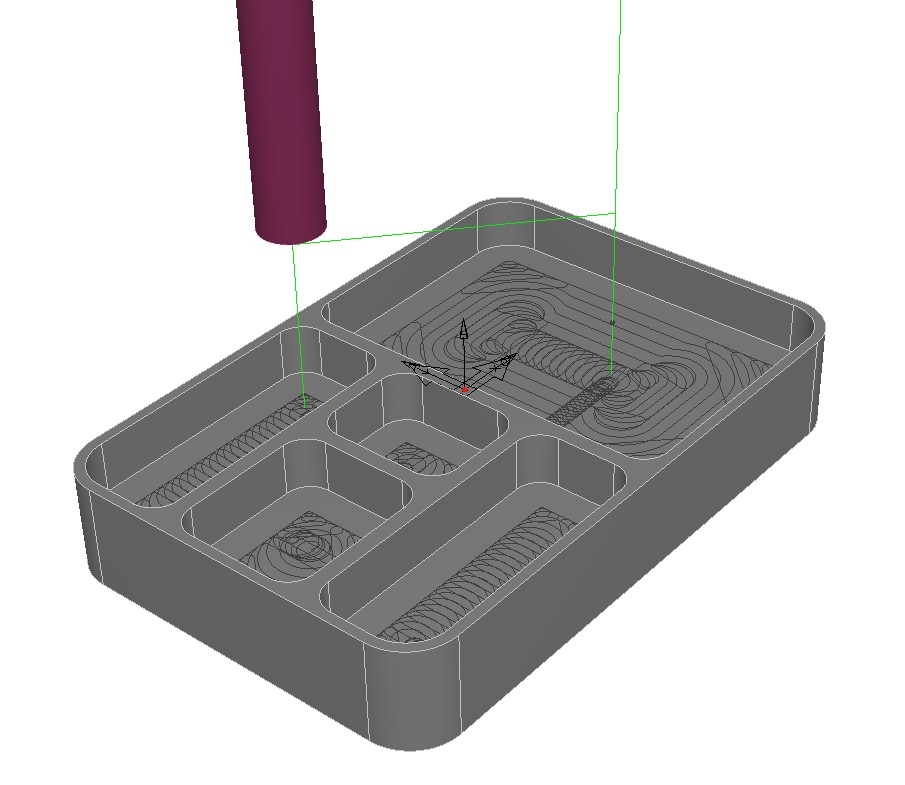
2.5D Features and Improvements
2D Vortex Pre-Drilling
A Pre-Drilling operation can now be added as an entry move, for the 2.5D Vortex cutting strategy. This is particularly useful when using solid carbide tools for your vortex roughing, that do not handle ramping into material well. The option is set within the strategy page, with the additional drilling features appearing in the operations list, and the locations of each pre-drill being determined automatically.
3 Axis Features and Improvements
3 Axis Vortex Pre-Drilling
A Pre-Drilling operation can also be used as an entry move for the 3D Vortex cutting strategy. This is particularly useful when using solid carbide tools for your vortex roughing, that do not handle ramping into material well. The option is set within the leads page, with the additional drilling features appearing in the operations list, and the locations of each pre-drill being determined either automatically, or with a point or curve definition.
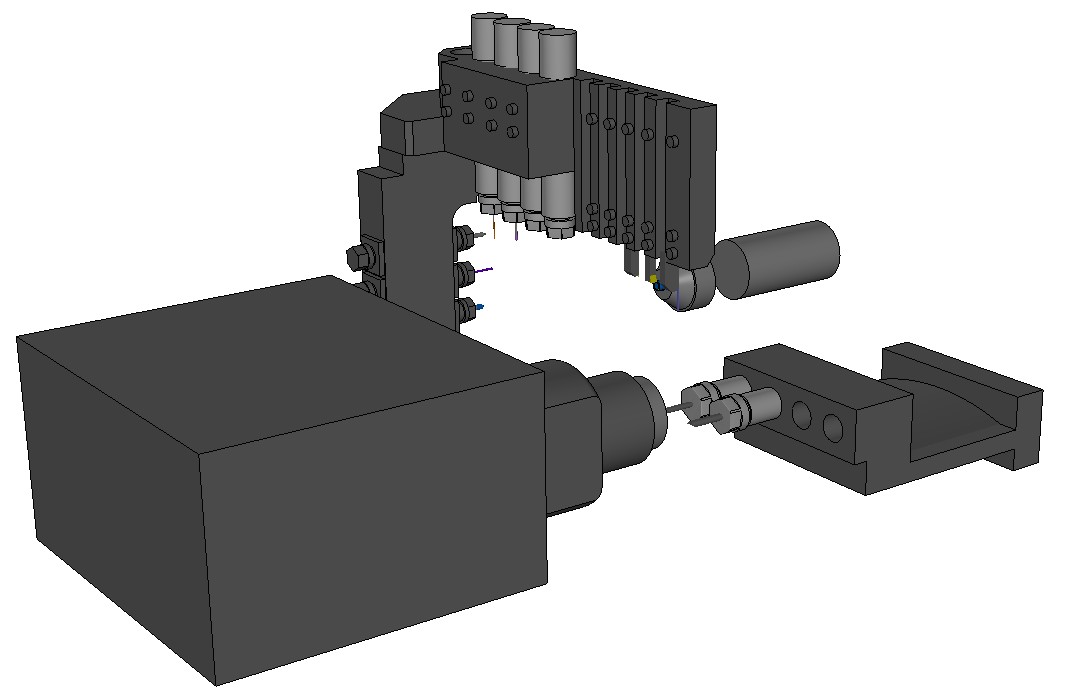
Turn/Mill Features and Improvements
Swiss-Type Lathe Support
FeatureCAM now supports Swiss-Type lathes; turning centres designed for the production of small, precision components. To create a Swiss project, a new document type is available with a range of Swiss functions, drag and drop synchronisation, full machine and sliding headstock simulation and more. Automatic tool mapping to slots is also available, where tools are assigned to slots that can only accept that type of tool.
May 2016:
FeatureCAM 2016 R3 - Is released.
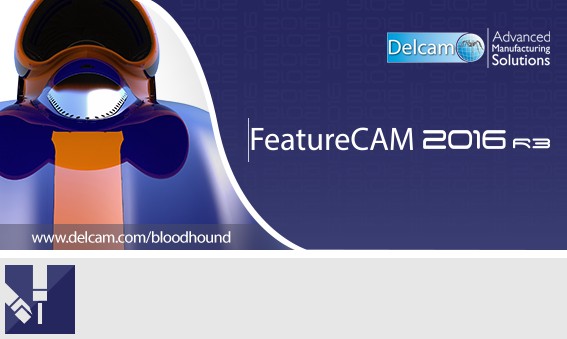
FeatureCAM 2016 R3 delivers a wide range of new features and improvements including new toolpath strategies and automatic control of the rotational axes on your machine.
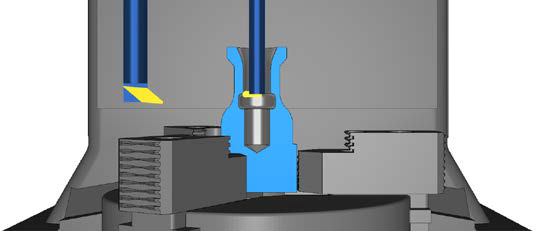
New features and enhancements include:
Automatic Index Rotation
Turning Heads With Two Tools
Spiral Face Milling
User Interface Improvements
Autodesk A360
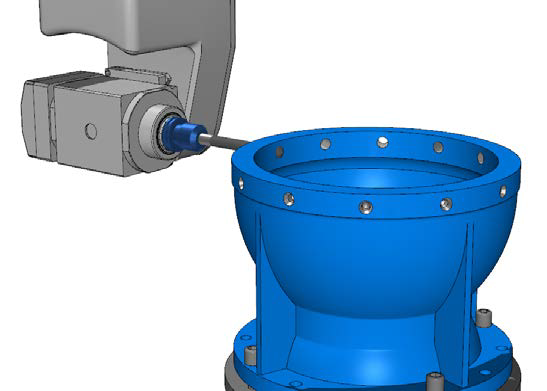
Automatic Index Rotation
Automatically control the rotation of your machine axes during indexing or 3+2 machining. Use machine limits from your machine design file, specify your own custom limits or choose the shortest rotation the machine can take.
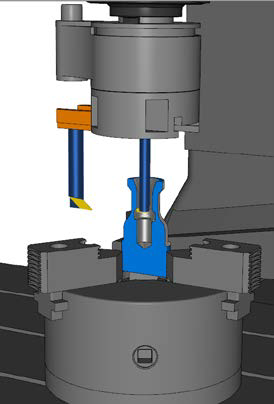
Turning Heads With Two Tools
Turning heads are tool holders that enable turning operations when used on a milling machine. You can now program two tools mounted to the same turning head tool holder.
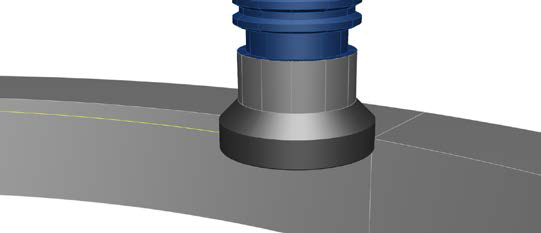
Spiral Face Milling
Create facing toolpaths using a spiral type toolpath. Depending on your part shape, this can reduce air cutting for a more efficient toolpath.
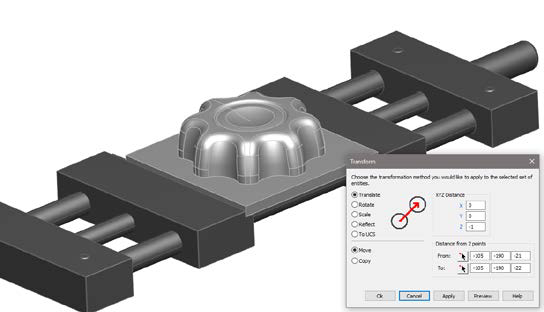
User Interface Improvements
Use a new apply button within the transform dialog and navigate quicker to feature coolants from the results tab. Use a new feature tab for post-processor variables and experience better simulation speeds.
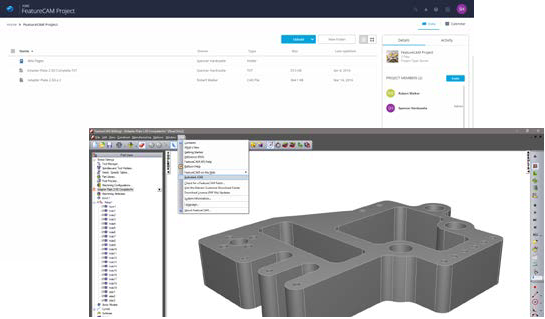
Autodesk A360
Access Autodesk A360 directly from FeatureCAM. A360 enables project collaboration, file viewing and file sharing, within a single, central workspace.
January 2016:
FeatureCAM 2016 R2 - Is released.
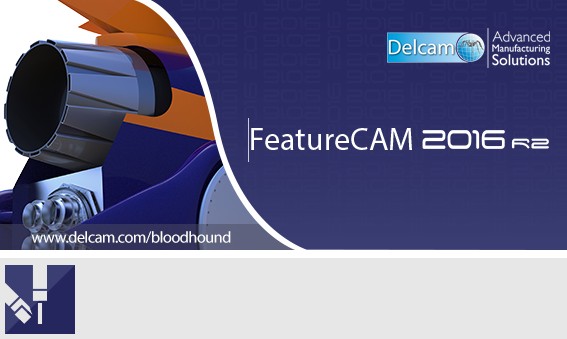
FeatureCAM 2016 R2 delivers a wide range of new features and improvements including more 5-axis functionality, as well as added control and simulation capabilities for multi-axis machines.
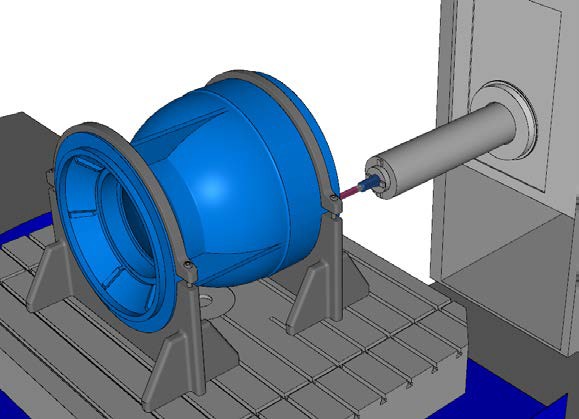
Automatic Tool Selection Improvements
W-Axis Support
Post Processor Documentation
Machine Design File Selection
Relative Plunge
Curve Sorting for 2.5D Pocket Features
Z-Axis Indexing in 5-Axis Part Documents
Turret Control in Simulation
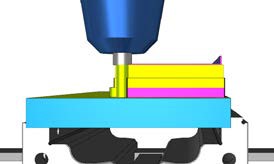
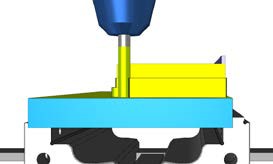
Automatic Tool Selection Improvements
Take into account the tool shank diameter during automatic tool selection. If the shank is larger than the tool cutting diameter, FeatureCAM will choose an appropriate tool to prevent gouges of your tool shank and part.
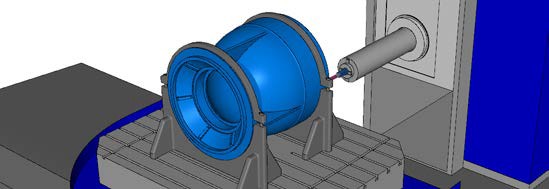
W-Axis Support
Control and simulate moveable live spindles (W-axis) for machine tools such as horizontal boring machines. This can be used to extend the travel limits of the Z-axis, to avoid collisions.
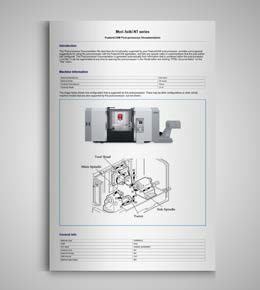
Post Processor Documentation
Automatically generate a simple HTML guide, which describes the functionality of the currently loaded post processor. From this, you can immediately understand the capabilities of the post processor.
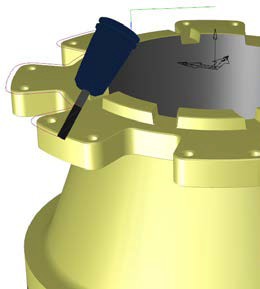
Machine Design File Selection
Select and view machine design files at a document level. This reduces programming time for full machine simulation.
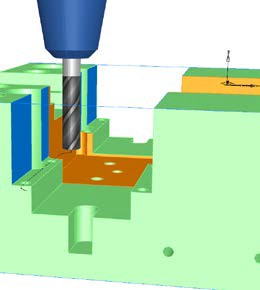
Relative Plunge
Set a relative plunge to allow the tool to rapid to the plunge clearance location, rather than feed to it. You can now use this option for 2-axis spiral and zig-zag toolpaths, to reduce machining time.
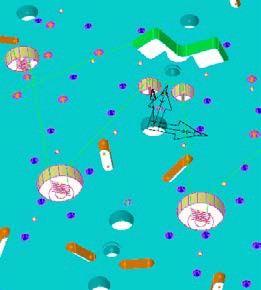
Curve Sorting for 2.5D Pocket Features
Control the machining order of multiple curves within a single feature. This is automated using various options including ascending and descending in X,Y or Z or using the shortest path to achieve the quickest time.
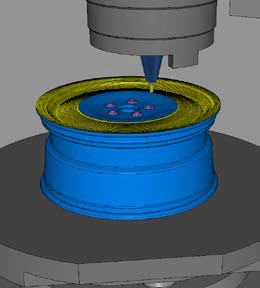
Z-Axis Indexing in 5-Axis Part Documents
Machine features aligned to the Z-axis using the C-axis (rotating about Z), in a 5-axis document. This can decrease machining time, improve surface finish and avoid travel limits of machines.
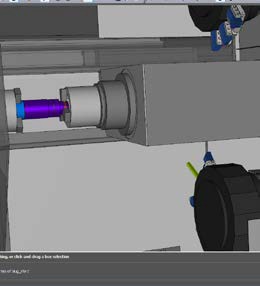
Turret Control in Simulation
Simulate and control the index position of a turret during a part handling feature. This lets you visualise the correct index position during machine simulation to ensure no collisions.
September 2015:
FeatureCAM 2016 R1 - Is released.
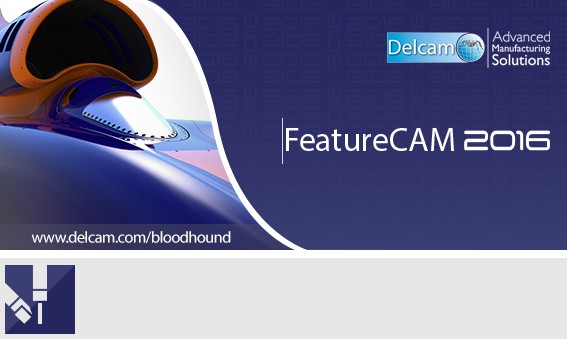
FeatureCAM 2016 delivers a wide range of new features and improvements including added control for 2.5D groove features, reductions in the machining time of 2.5D and 3D Vortex toolpaths and dynamic stock models for 3D roughing.
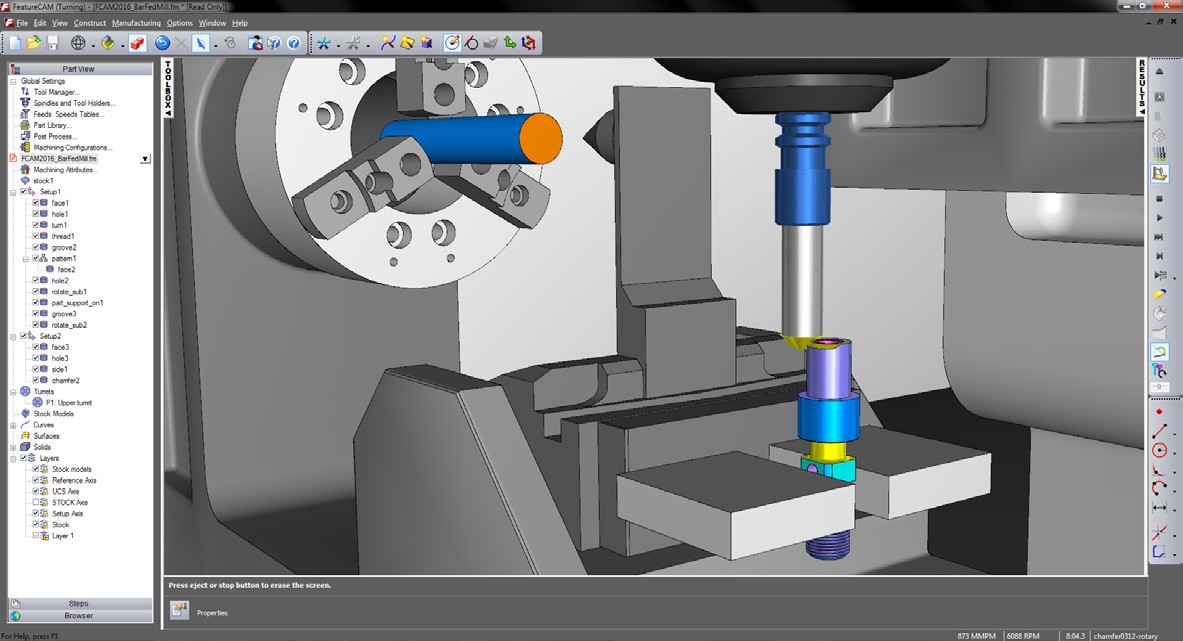
User interface improvements
FeatureRECOGNITION setup creation
Nesting
Autodesk RealDWG Import
New Inside/Outside Groove toolpath
2.5D and 3D Vortex non-cutting moves
Dynamic stock for roughing
Swarf Z limits
Bar fed mills
Realistic turning heads
Automatic tool orientation
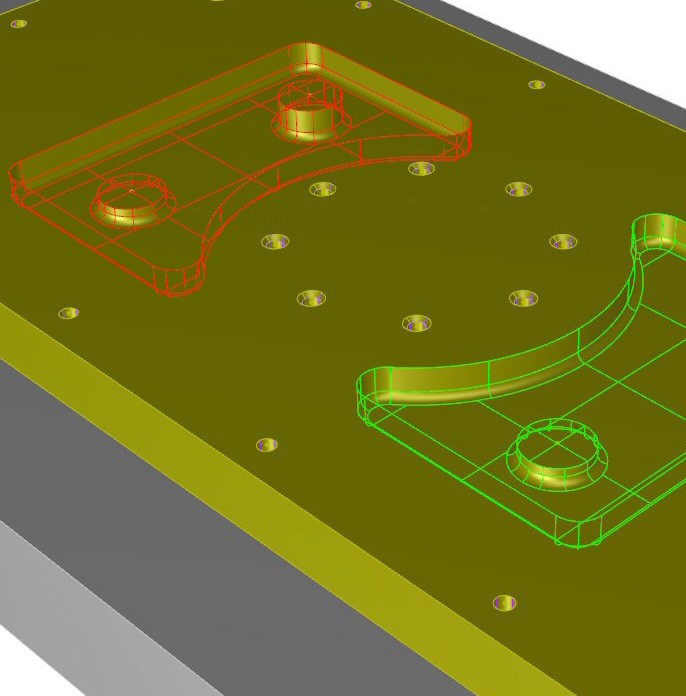
User Interface Improvements
Highlight part view items with your cursor in the graphics screen to quickly and easily find and select desired items. Additionally, change the tool colour during simulation with a toolbar button or menu item.
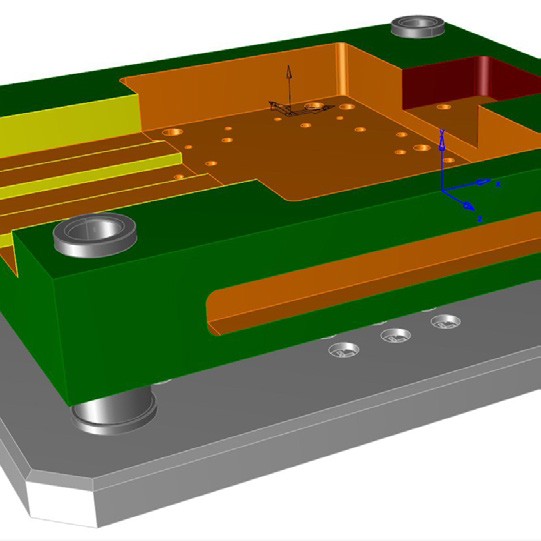
FeatureRECOGNITION Setup Creation
Reduce your programming times by rapidly creating additional setups during FeatureRECOGNITION via a new button in the Feature Wizard.
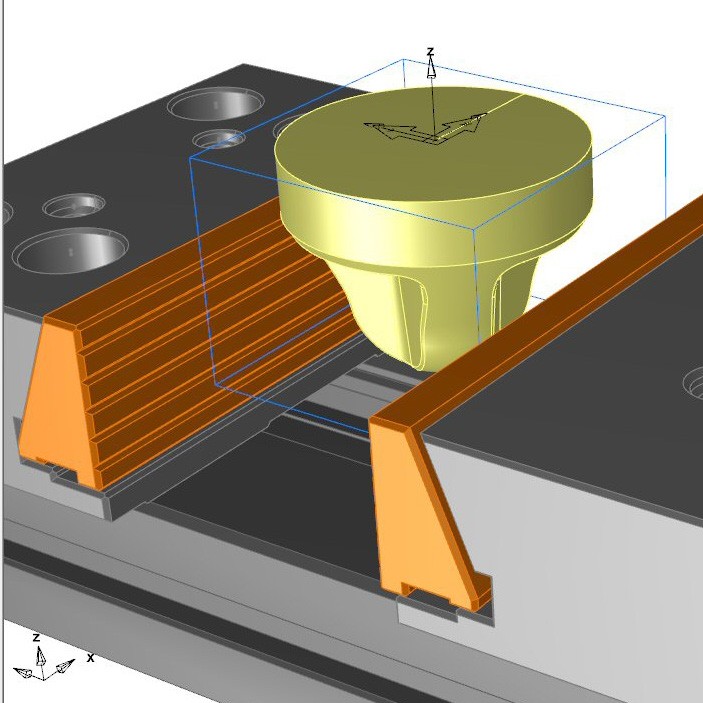
Vice Import And Alignment
Quickly import and align predefined vices and chucks into your FeatureCAM project. This helps reduce your programming times and improves collision checking, by automatically setting imported devices as clamps.
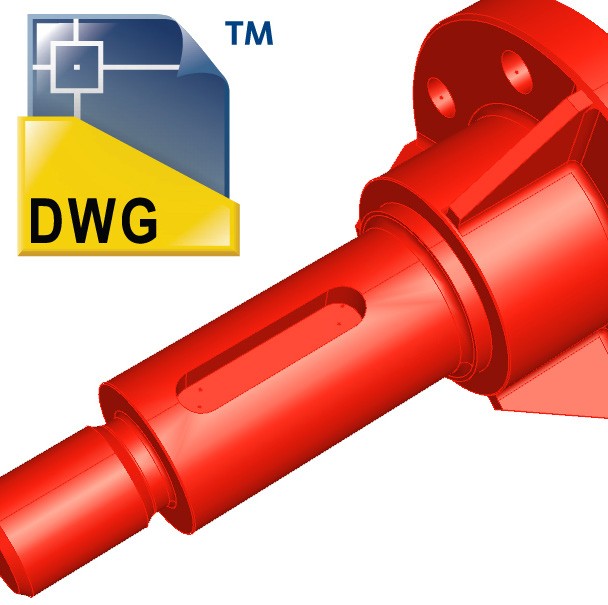
Autodesk RealDWG Import
Quickly import Autodesk RealDWG files into FeatureCAM and benefit from support for DWG solid model import.
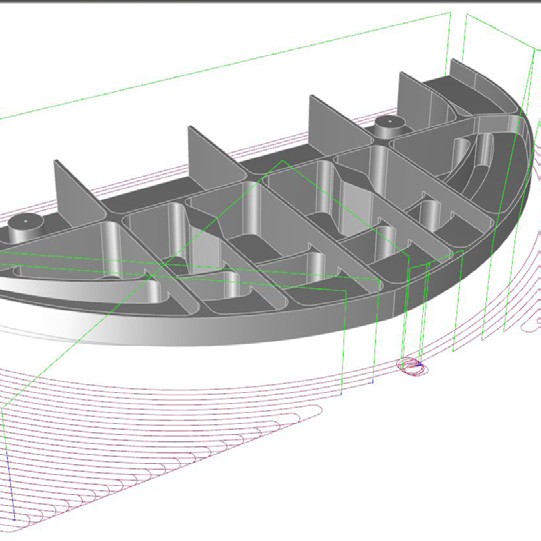
Vortex Non-Cutting Moves
Adjust the non-cutting moves of your 2.5D and 3D Vortex toolpaths, with options to retract and lift or increase the feedrate, to optimise your toolpaths and reduce cutting time.
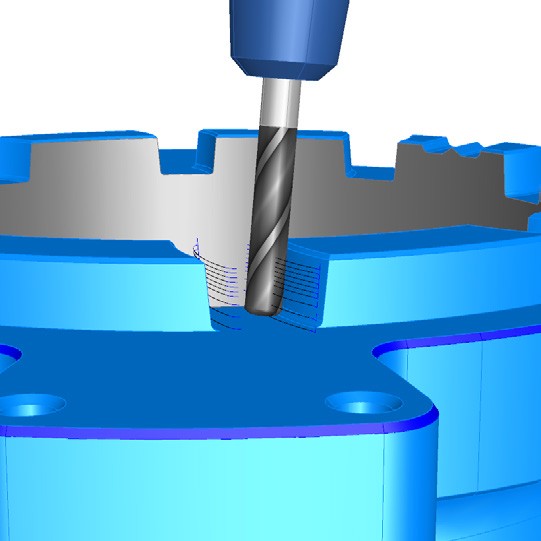
Swarf Z Limits
Control the upper and lower Z limits of a 5-axis simultaneous swarf toolpath to overcome tool length limitations, or when you wish to vary the stepdown for different segments of the swarf.
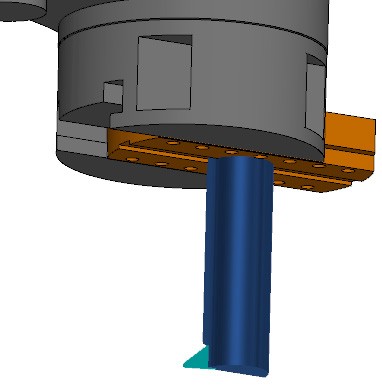
Realistic Turning Heads
Define more complex turning head tool holder models in the Machine Design file, and assign your tools to the holders via the tool mapping.
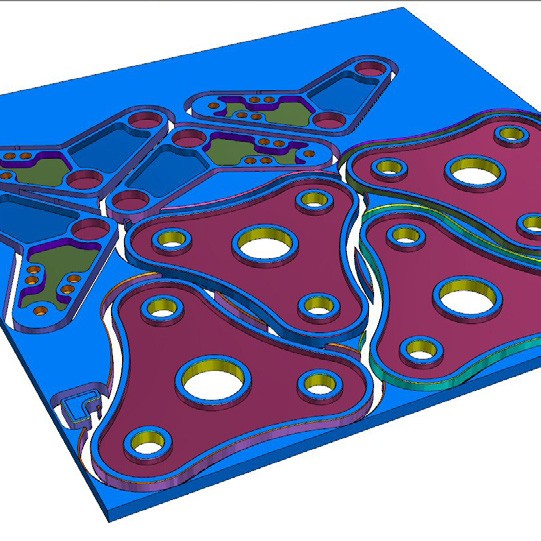
Nesting
Use FeatureCAM with PowerSHAPE to select your machining files and nest them in a single block to maximise stock material usage efficiency.
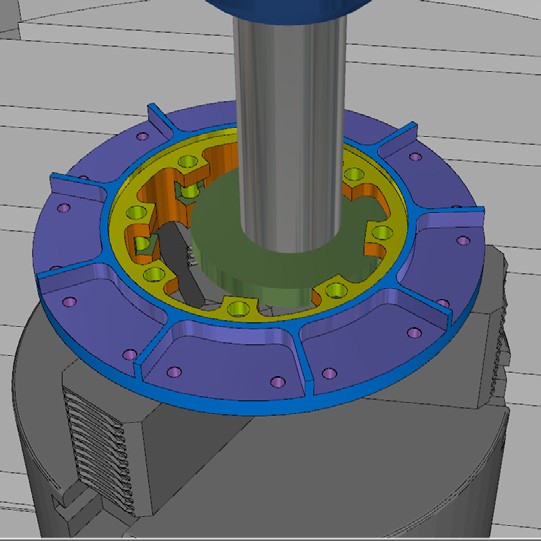
New Inside/Outside Groove Toolpath
Fine-tune your Inside/Outside Groove toolpaths with new options for rough stepover type, wind-fan and start points for finishing, and gouge checking for plunge and retracts, in addition to support for tool radius and partline cutter compensation.
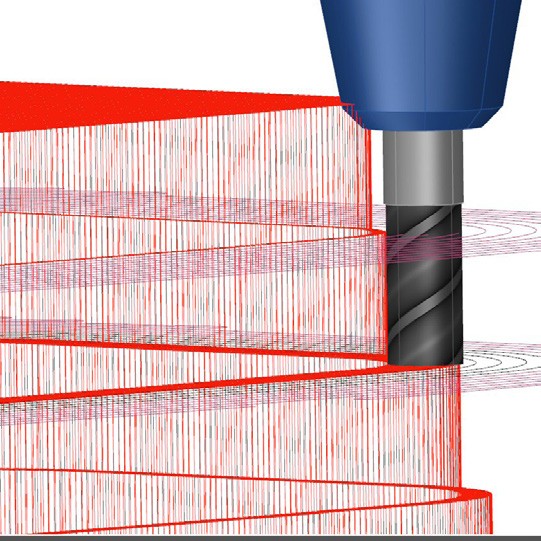
Dynamic Stock For Roughing
Keep your Z-Level Roughing toolpaths completely free of tool holder collisions by taking into account any remaining stock on a model, with Holder Collision Clipping.
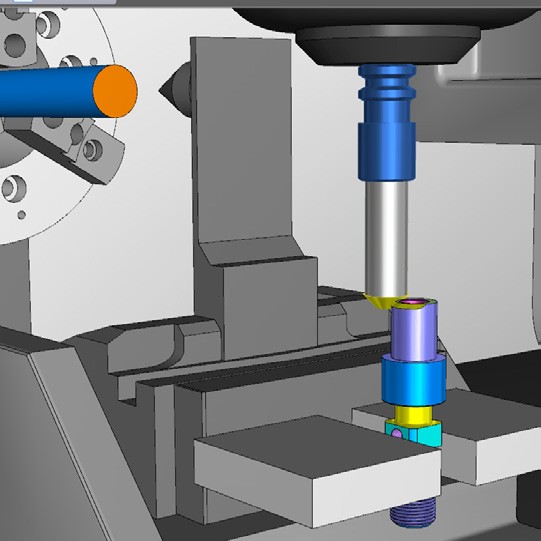
Bar Fed Mills
Program your multi-tasking bar-fed milling machines with FeatureCAM. Access the back working area by setting the swivel angle, and utilise cut-off operations that use milling tools.
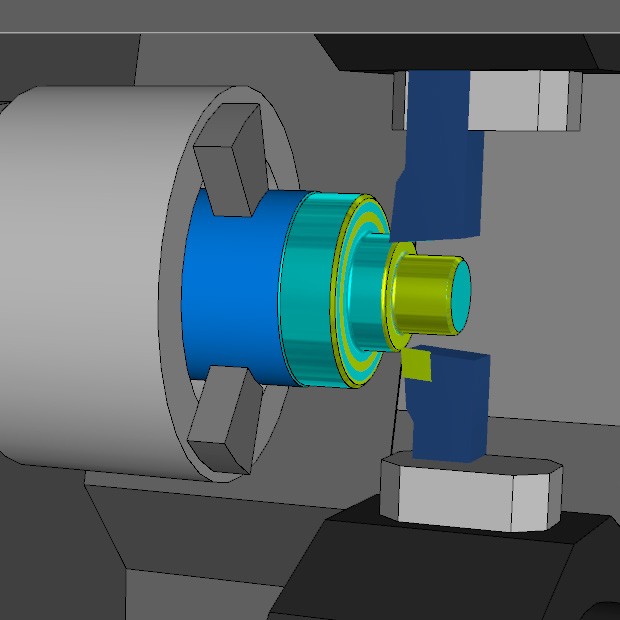
Automatic Tool Orientation
Simplify the turning tool selection process with the ability to automatically use a single tool in multiple orientations, minimising your tool crib size and reducing the time taken to program parts.
May 2015:
FeatureCAM 2015 R3 - Is released.
FeatureCAM 2015 R3 delivers a wide range of new features and improvements including greater control over 5-axis operations and more comprehensive tool support in turning. Safety and workflow efficiency have been enhanced with better collision clipping, machine simulation limits and a new selection method.
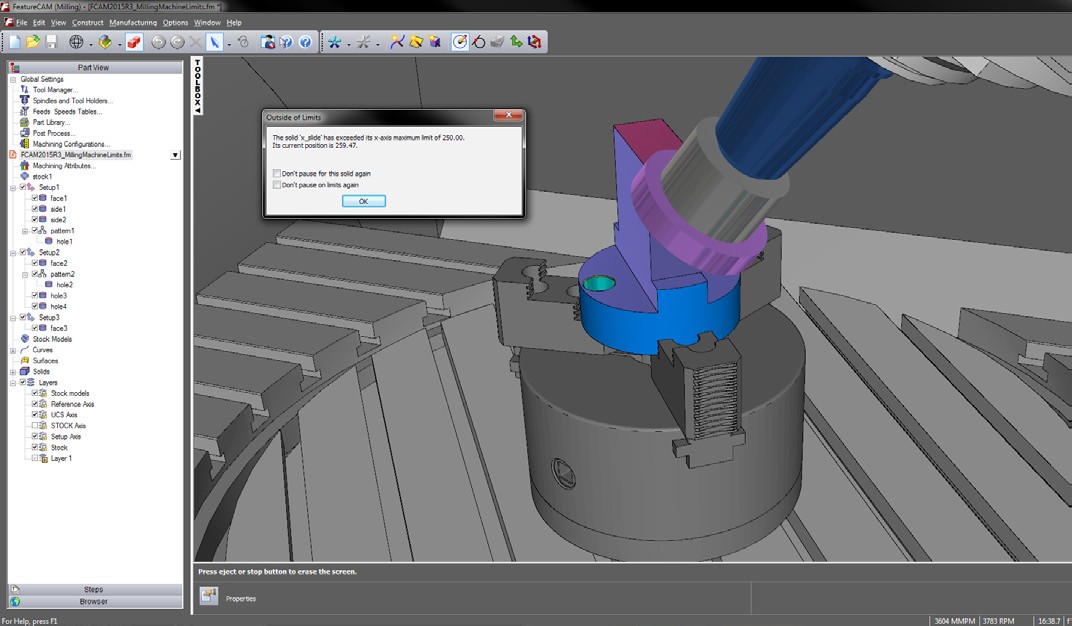
New features and enhancements include:
Milling Machine Limits
Turning Machine Limits
Partial Box Selection
Accurate Shank and Holder Collision Clipping
Index Limit Calculation from Machine Attributes
5 Axis 2D Spiral
Turning Head Holders
Mini Turrets
Orientation Angle
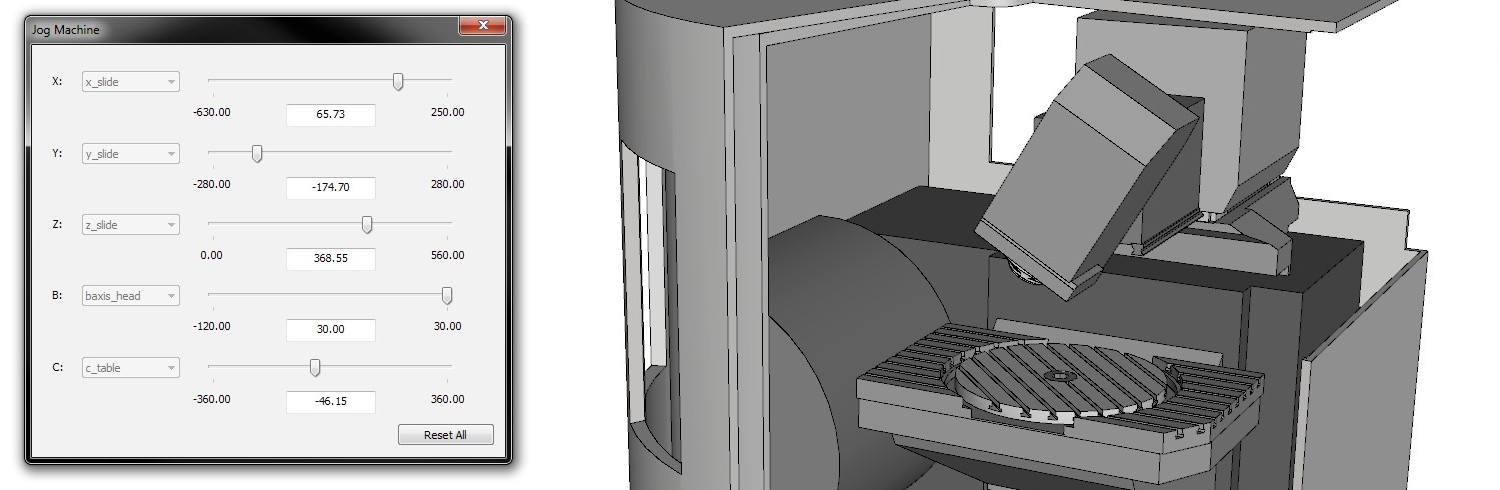
Milling Machine Limits
Milling limits have been added to allow you to set physical constraints for 3, 4 and 5-axis milling machine simulation models. Setting the limits for the linear and rotary machining axes saves time and money, while improving safety by checking the machining range before part production.
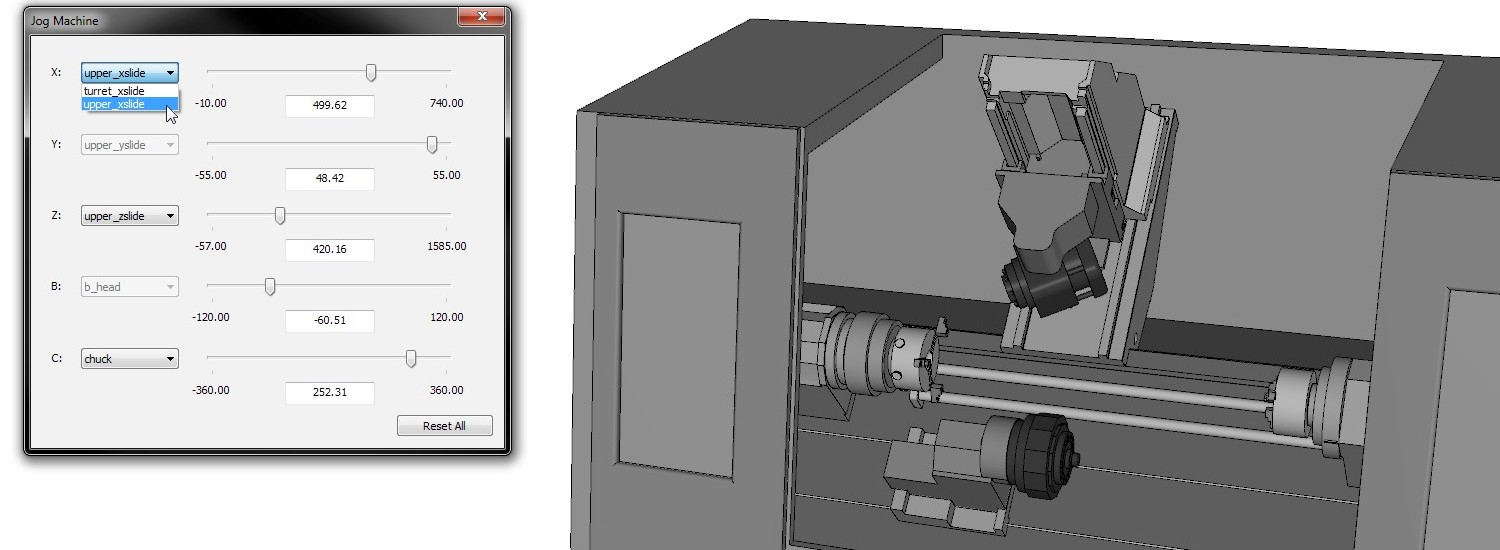
Turning Machine Limits
In addition to milling limits, limits are also supported in turning and turn/mill, including machines with multiple turrets and spindles. This means the machining range of even your most complex machines can now be checked before manufacturing begins.
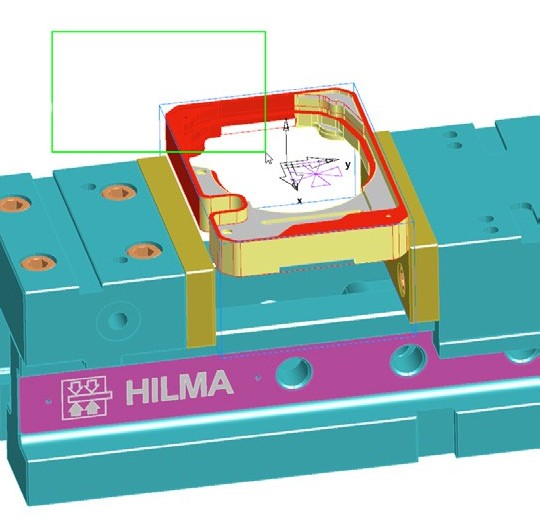
Partial Box Selection
Selecting components within your model has been made even easier with the addition of partial box selection. Adding to the fully contained and drag selection modes, this new mode allows you to box select partially and fully enclosed entities at once, maximising your workflow efficiency.
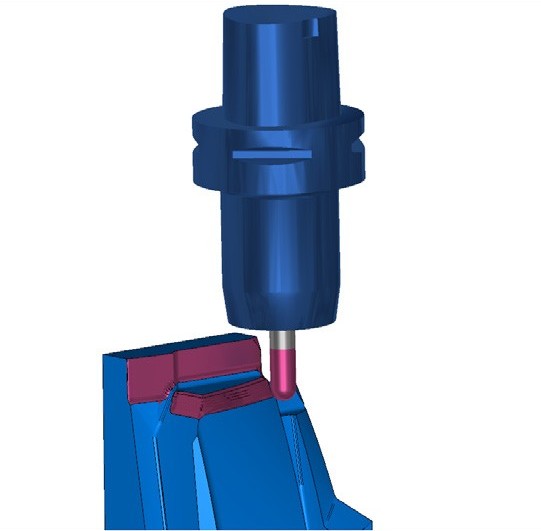
Accurate Shank and Holder Collision Clipping
In addition to the parameter-based holders, 3-axis collision checking has been enhanced with the ability to clip toolpaths when using holders derived from curves and solid models. This results in safer machining and easier programming, as a more accurate representation of the holder can now be used.
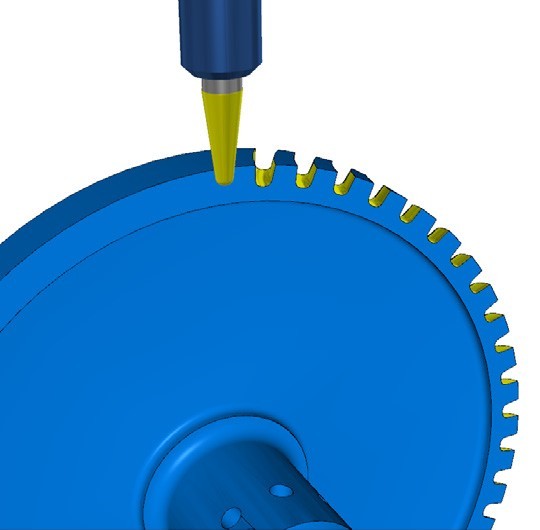
Index Limit Calculation from Machine Attributes
The ability to change the method of calculating the index limit is now available from the machining attributes dialog. This option calculates the limits based on the size of the solid revolve resulting in an index clearance more efficiently close to the model.
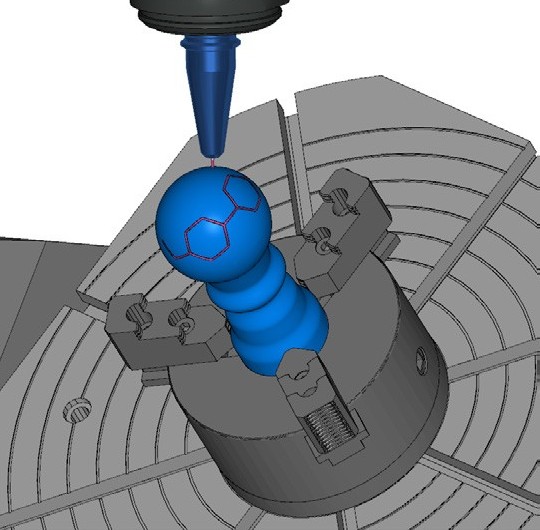
5 Axis 2D Spiral
Support for 5-axis is now available in 2D spiral operations, giving better control of the tool axis. Spiral 2D wall only toolpaths for example, can benefit from 5-axis options, ensuring uniform depth of cut and cross section while engraving.
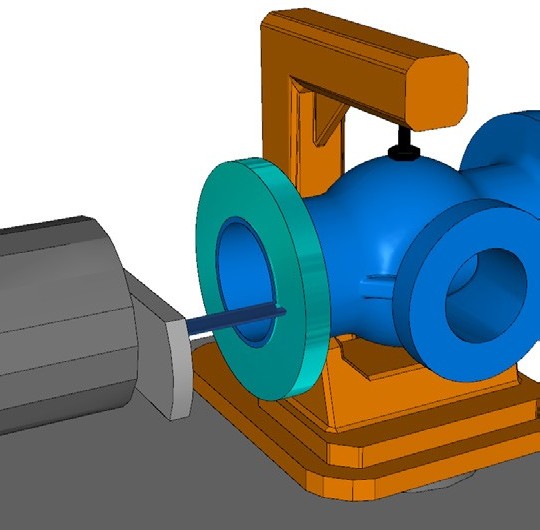
Turning Head Holders
A new add-in allows FeatureCAM to support special tool holders that can turn when used on a milling machine, known as turning heads.
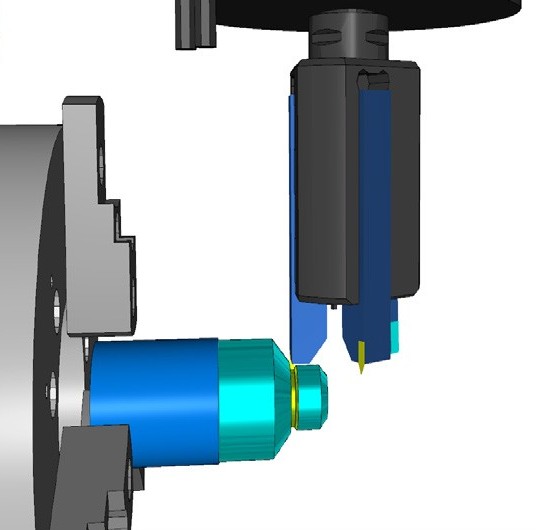
Mini Turrets
The ability to program mini turrets, which allow more flexible tool positioning and faster tool changes on the machine, can now be programmed in Turn/Mill when used in conjunction with a B-axis head. This allows for more accurate simulation and NC code generation within FeatureCAM.
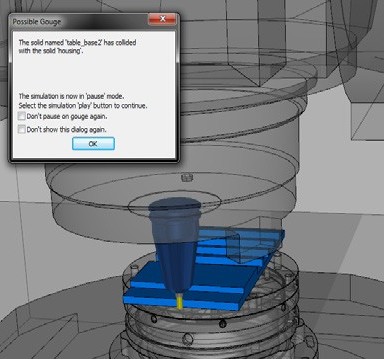

Orientation Angle
More control is now available during 5-axis part programming with the ability to set the C-axis orientation about the Z-axis. This new feature helps avoid possible machine collisions and over travel, making programming safer and more efficient.
January 2015:
FeatureCAM 2015 R2 - Is released.
FeatureCAM 2015 R2 provides a wide variety of improved functions, including a major new Addin, enhancements to automatic tool selection and solid modelling developments. A new Vortex approach method, as well as the 2, 3 and 5 axis output option modifications, create our best release of FeatureCAM to date.
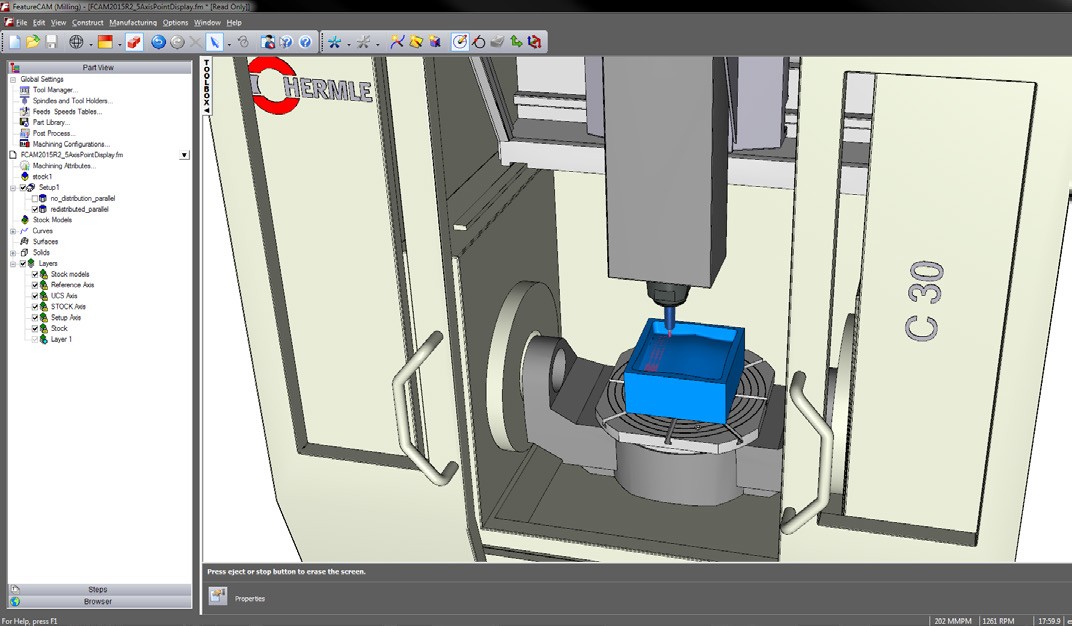
New features and enhancements include:
New Flat Approach for Vortex
Multi Tool Block Definitions
Output for NT and Vortex Toolpaths
3 and 5 Axis Toolpath Point Display
Vortex Milling Calculator Addin
Drilling Pecking Depth Per Tool
Automatic Tool Selection Attributes
Combining Multiple Solids
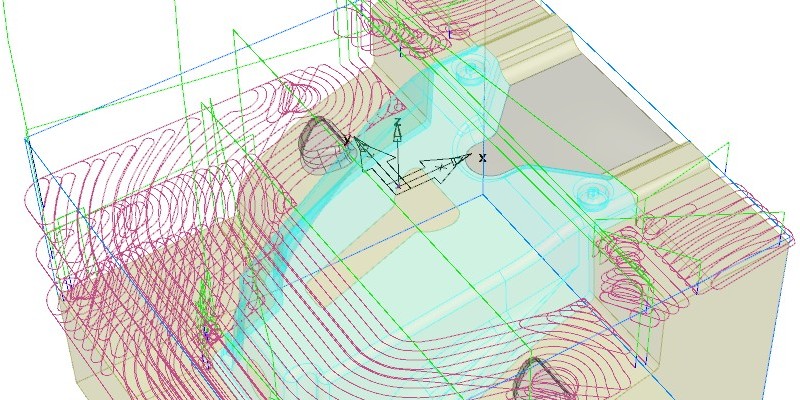
New Flat Approach for Vortex
Vortex toolpaths are now more efficient, when machining flat areas, as they allow an approach from outside the stock. Flat sections are now extended, until they reach a pre-machined area, removing the need for helical entry moves.
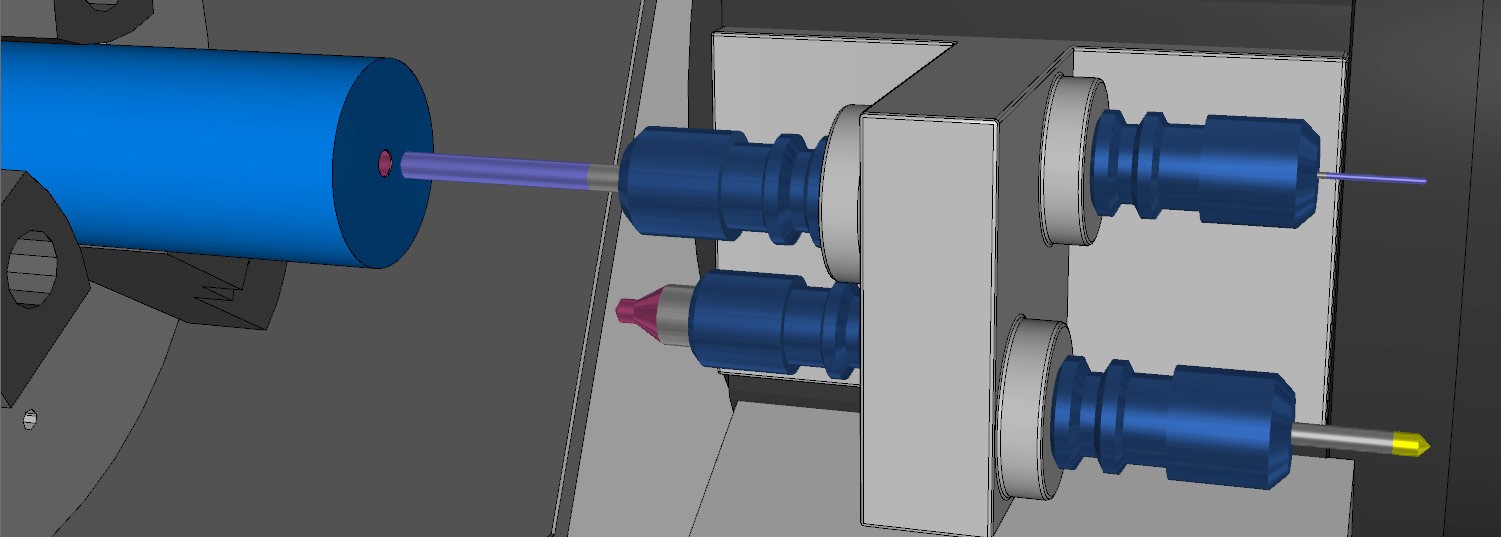
Multi Tool Block Definitions
Multi Tool blocks can now be created within Machine Design files. These tool blocks now have a list of tool locations, with attributes describing the type of tool to be held in each location, and can now be selected within the tool mapping window.
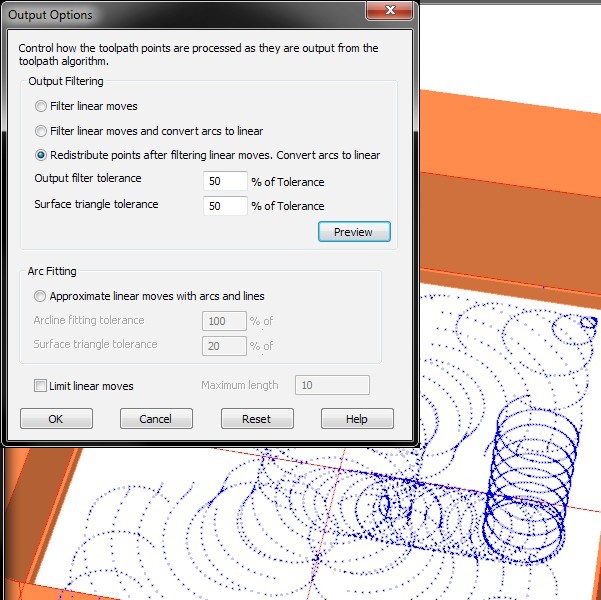
Output for NT and Vortex Toolpaths
Output options are now available in 2 Axis NT and Vortex toolpaths. Control over point filtering and arc fitting, essential for smooth machine motion, can now be set in the feature, with the distribution of toolpath points now displayable.
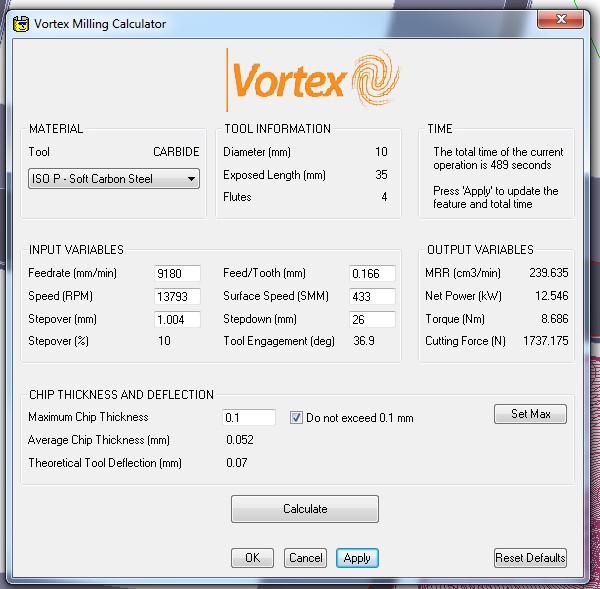
Vortex Milling Calculator Addin
Maximise your productivity and efficiency when machining with Vortex. This Addin interpolates tooling catalogue parameters, using maximum chip thickness control to reduce toolpath time, whilst maintaining the cutting load.
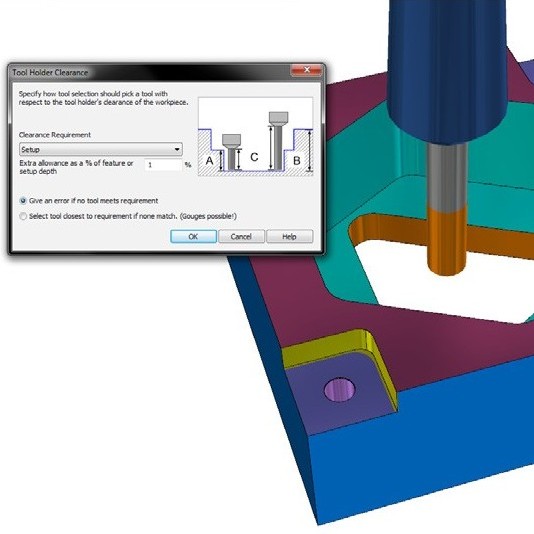
Automatic Tool Selection Attributes
Exposed length checking of the tool improves automatic tool selection, by allowing tools to be verified against feature depth or setup depth, to avoid potential collisions.
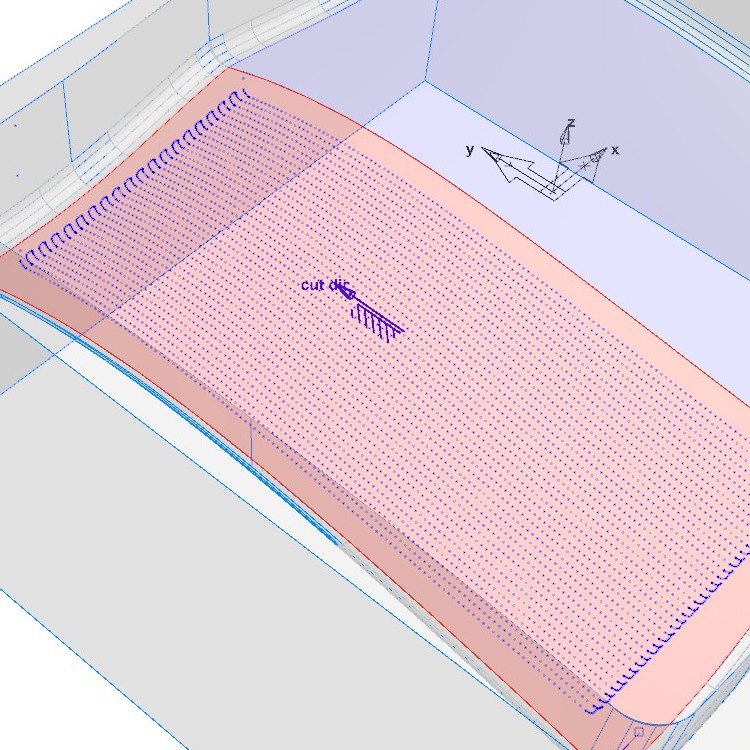
3 and 5 Axis Toolpath Point Display
Toolpath points can now be displayed via the output options dialog box. A new preview function allows the user to view the toolpath points to verify the desired output, helping to maximise the machine controller compatibility.
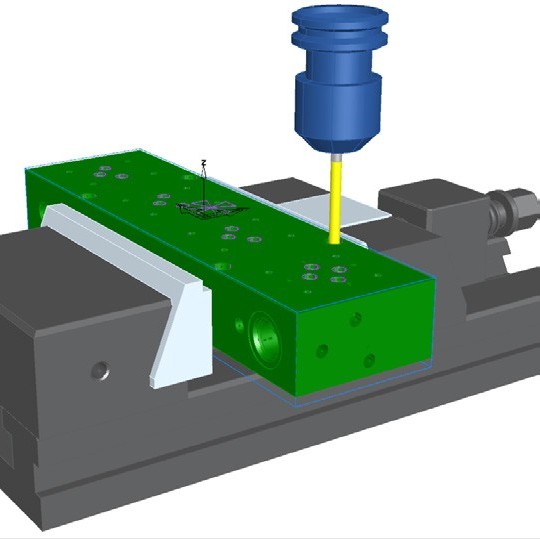
Drilling Pecking Depth Per Tool
The allocation of specific drill pecking depths on a per tool basis now streamlines FeatureCAM’s workflow. There is now no longer the need to update global pecking defaults after feature creation, significantly reducing the programming time for drilling.
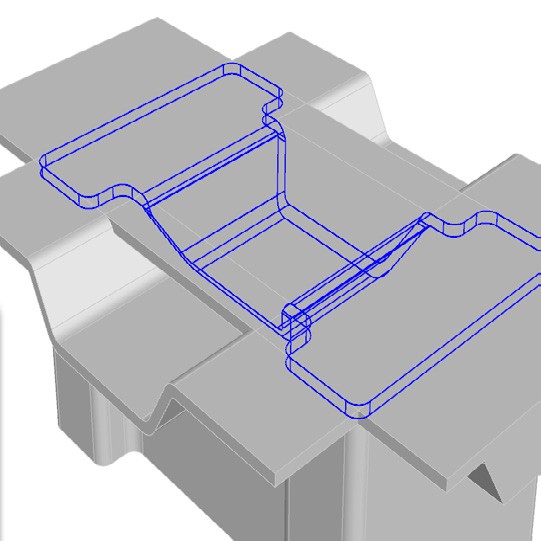
Combining Multiple Solids
Solid modelling is even quicker thanks to improvements in the Solid Combine function. Multiple solid models can now be combined at once as either Unions or Intersections.
October 2014:
FeatureCAM 2015 - Is here.
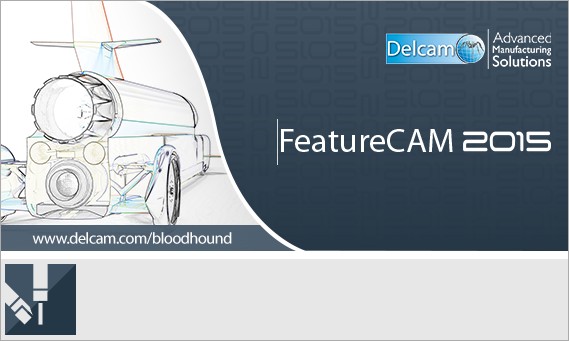
FeatureCAM 2015 brings a wealth of new features and functionality, with 3 and 5-axis safety and efficiency improvements, Wire EDM usability enhancements and FeatureRECOGNITION revisions to help reduce your programming times further.
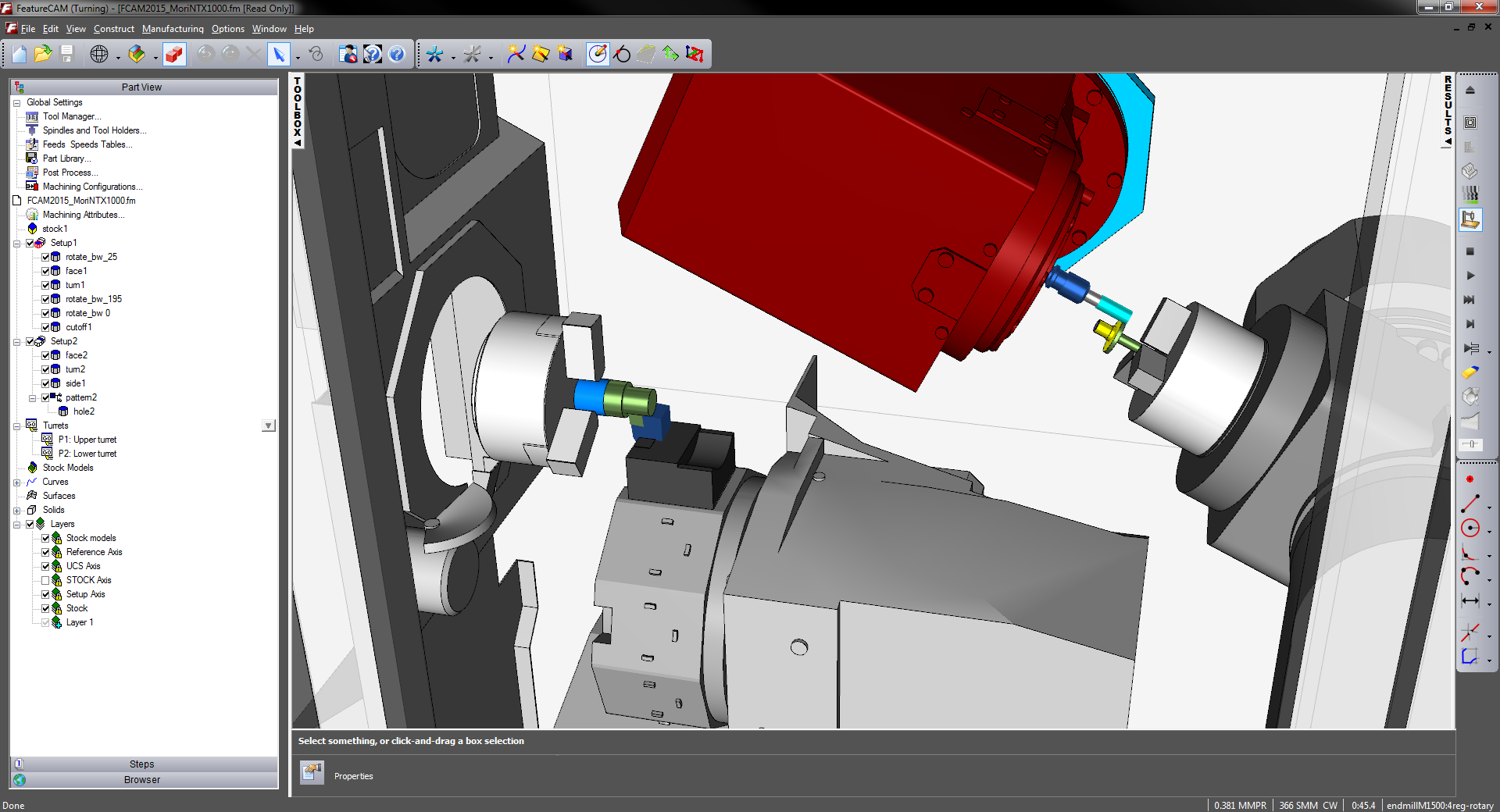
3-Axis Automatic Holder Collision Checking
Expanded Wire EDM Database
Stock Model & Boundary Combination
Machine Maximum Stock
Travelling Steady Rest
Multiple Face Feature Recognition
5-Axis Hole Patterns Around An Arbitrary Axis
Addins Library
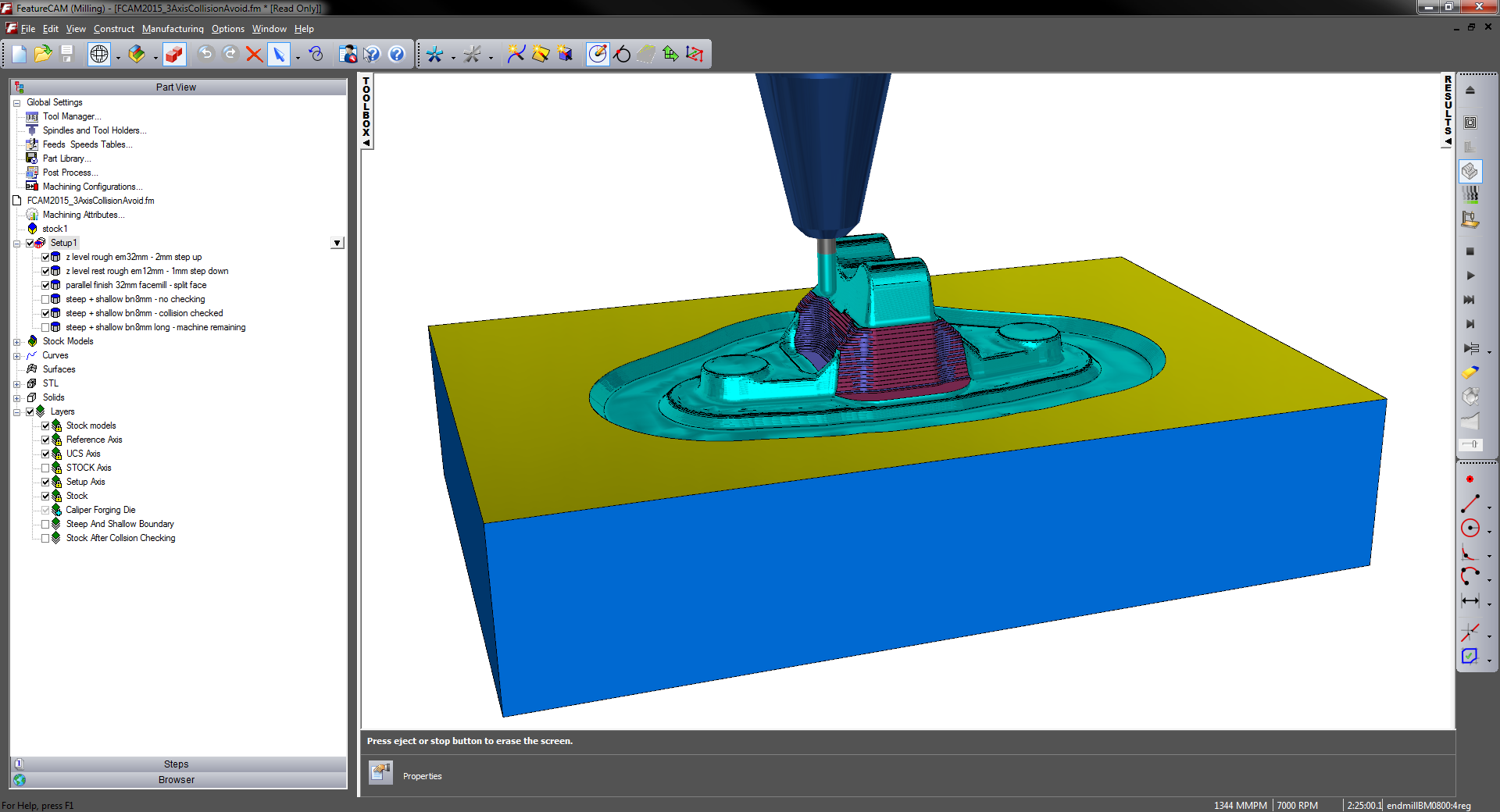
3-Axis Automatic Holder Collision Checking
Programming of complex parts is now even easier with the inclusion of Automatic Collision Checking of the tool shank and holder against the part.
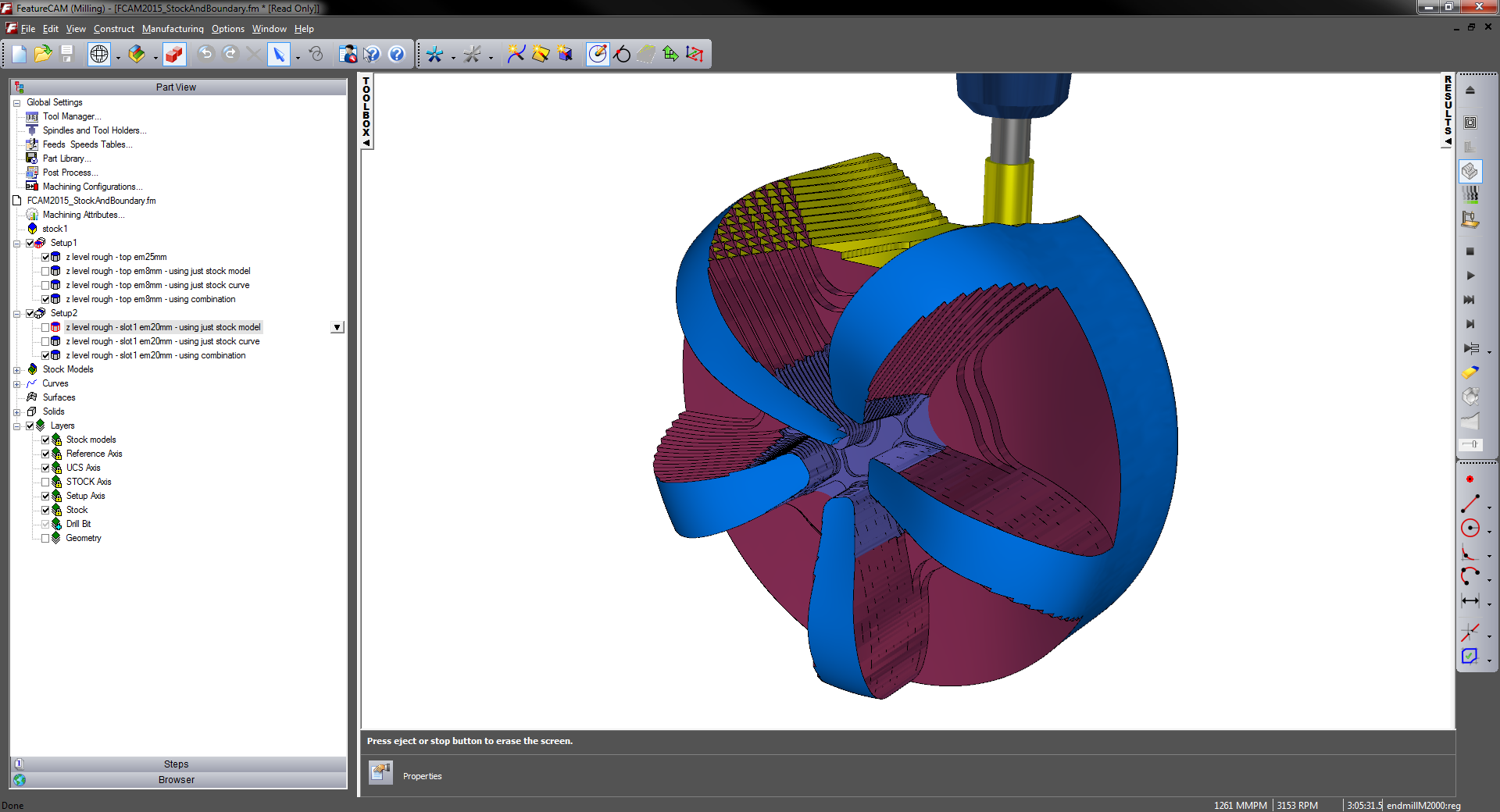
Stock Model & Boundary Combination
Combine stock models with the Part Surface Dimensions, the Stock Dimensions, Solid Models and Boundary Curves to machine parts more efficiently.
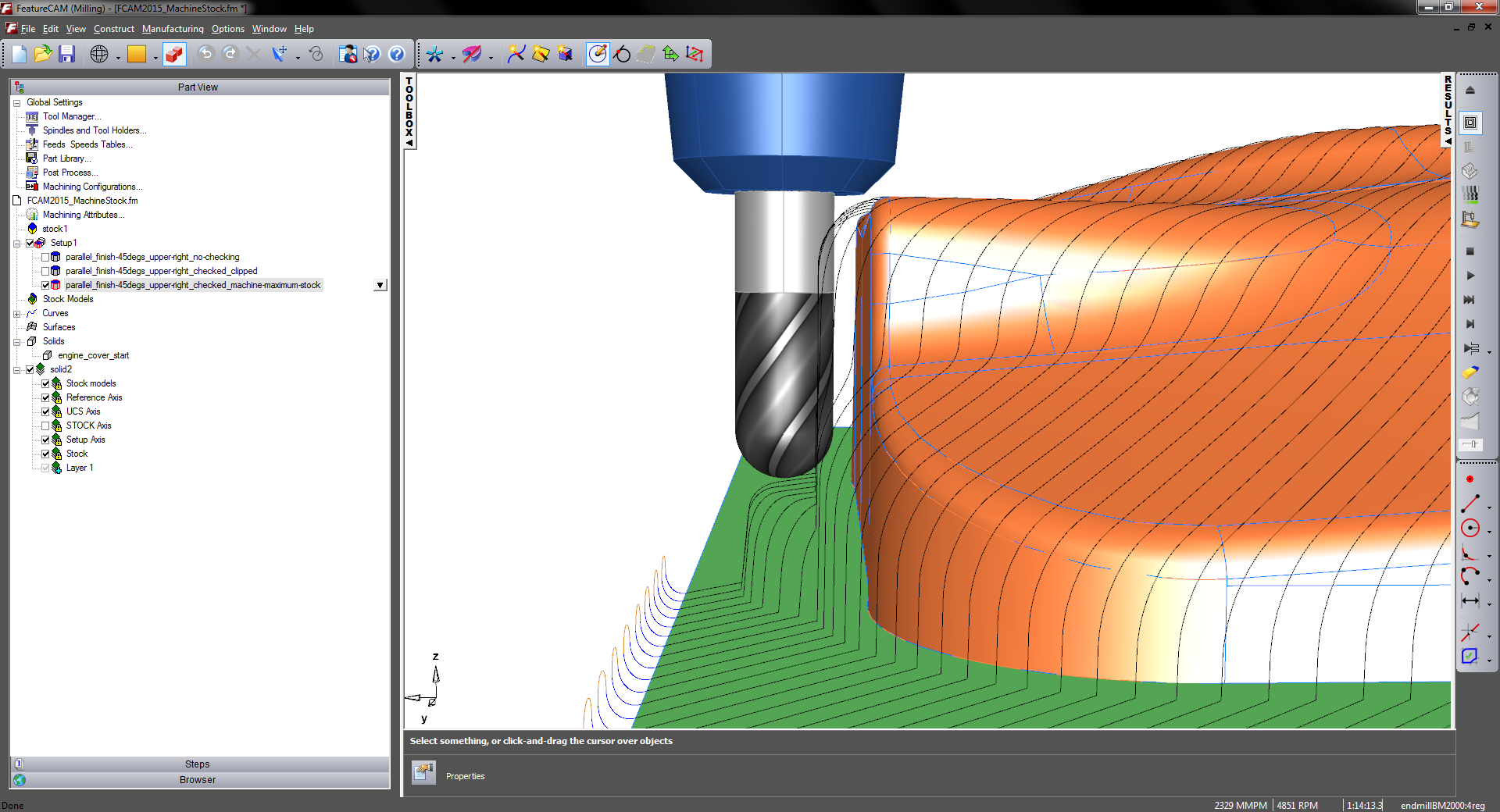
Machine Maximum Stock
Reduce the number of retractions by keeping the tool on the part to improve surface finish when used with Automatic Collision Checking.
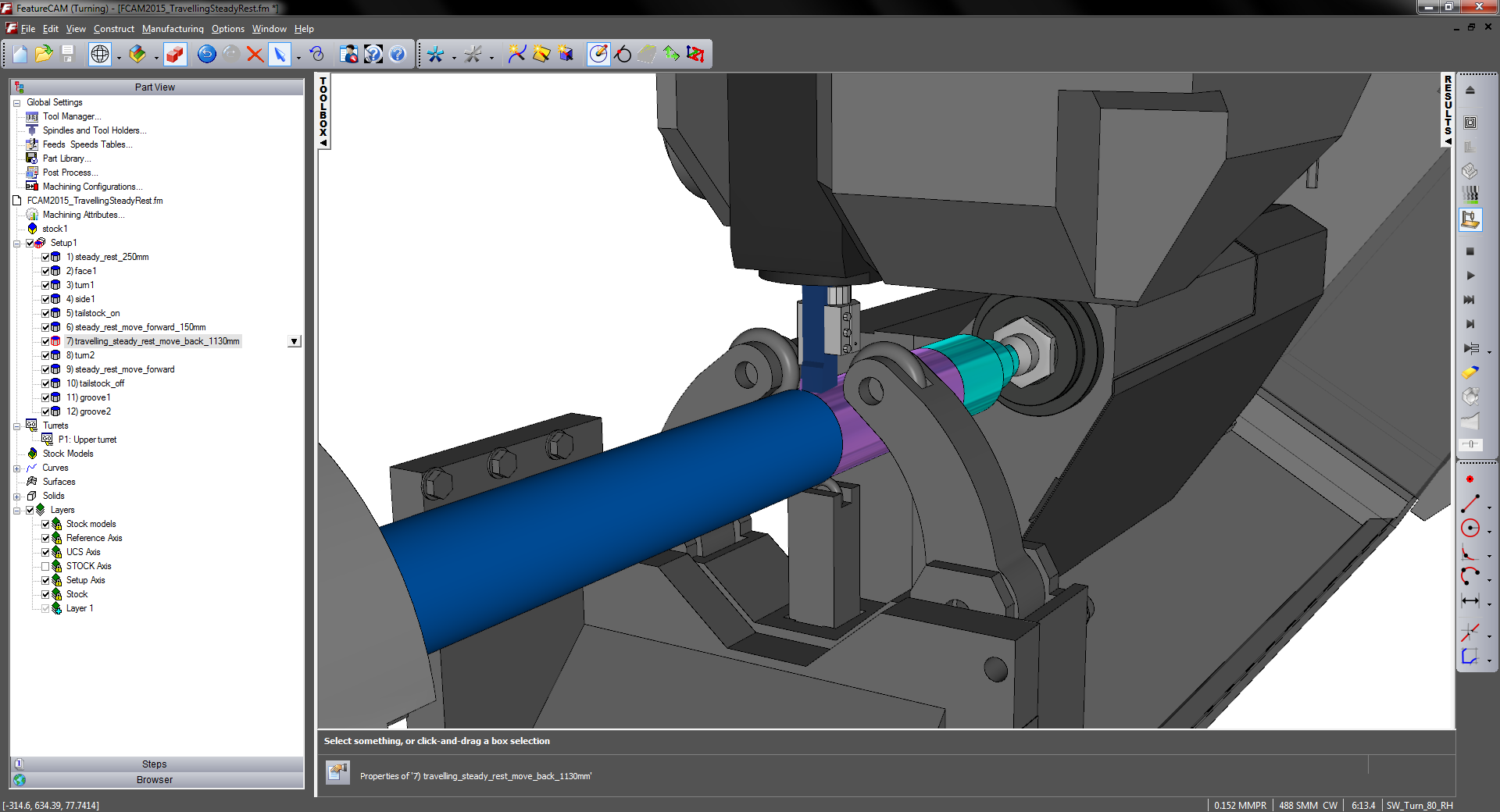
Travelling Steady Rest
Benefit from the ability to program travelling steady rests to support the workpiece, increasing the flexibility of programming very long turned parts.
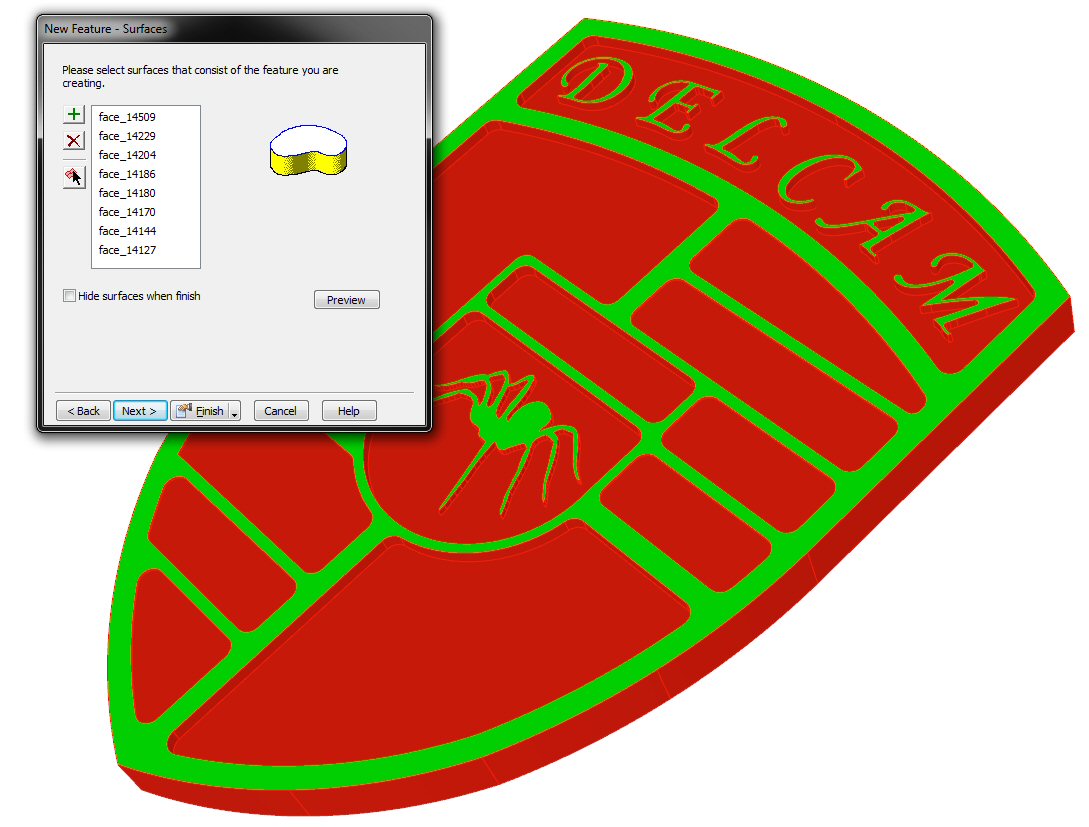
Multiple Face Feature Recognition
Avoid repeatedly creating face features by selecting multiple faces or surfaces when using Interactive FeatureRECOGNITION.
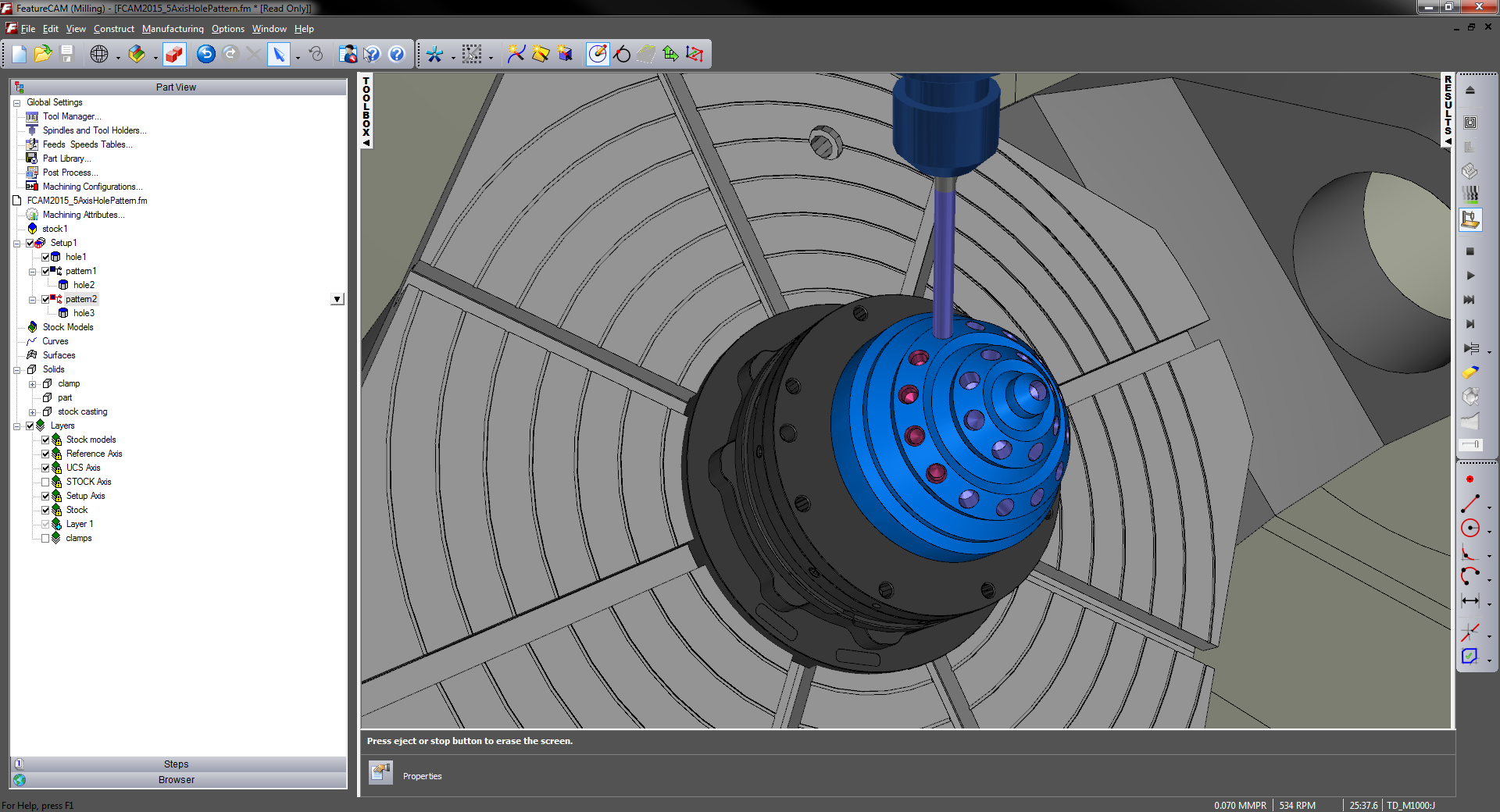
5-Axis Hole Patterns Around An Arbitrary Axis
Benefit from a new hole pattern definition to make programming 5-axis parts even easier, allowing changes to be made to multiple holes at once, reducing programming time.
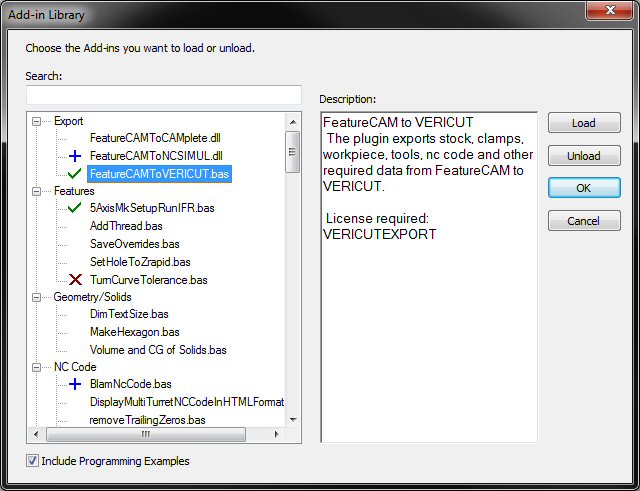
Addins Library
Benefit from streamlined access to the extensive library of published addins and programming examples as these are now incorporated into the distribution of the software.
Telephone: 0116 267 5588